I won’t bore you with how a watch works. Just watch some YouTube videos, and you’d learn it in a few minutes, and will be far more entertained.
Just briefly, in a quartz watch (right), there is a quartz crystal that sends out signals to a down counter to reduce its frequency to 1 Hz. This signal is fed into a coil to rotate a small gear to drive the watch. You could tell if you own a quartz watch or not if it uses batteries or if it’s dead silent, or if its second hand moves and stops in one second intervals.
If you own a mechanical watch its movement is most likely a modern balance wheel design (below) that operates by an oscillating balance wheel driven by a main spring that needs to be hand wound or is automatically wound when you move around your arm during your daily activities.
The mechanical watch is less accurate than the quartz watches but its second hand is far more interesting to watch because it has more emotion in it. It’s the difference between a mechanical music box, and a tune from your mobile phone.
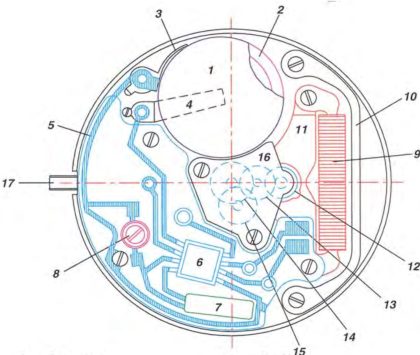
1. Battery 2. Insulator 3. Positive contact 4. Negative contact 5. Printed circuit 6. Integrated circuit 7. Quartz 8. Trimmer 9. Coil 10. Coil protector 11. Stator 12. Rotor 13-15. Train wheel 16. Train wheel bridge 17. Setting stem
As a technician, I prefer quartz watches because they are so easier to repair, and they have less mechanical wear, and they are dead accurate. As a mechanical engineer, and someone who loves astronomy I love mechanical watches because they connect me with Galileo.
If you live in Southern California, go visit the 5-meter Palomar telescope, and watch it through its glass door. Those who have Caltec or JPL badges could even get a permit to get in. There is a tall clock you could watch near the front door with a long pendulum. You could feel the telescope micro-turning in the background with every click of that clock. Telescope now use servo drives but imagine several tons of glass, and steel being the second hand of a mechanical clock.
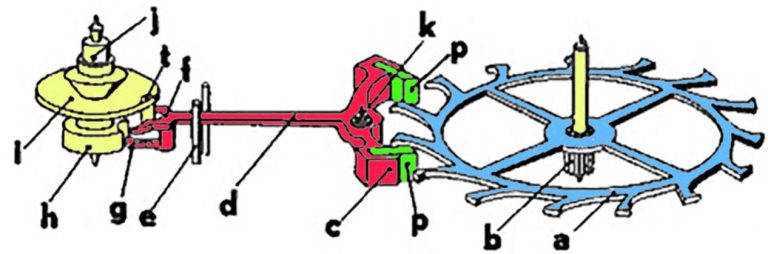
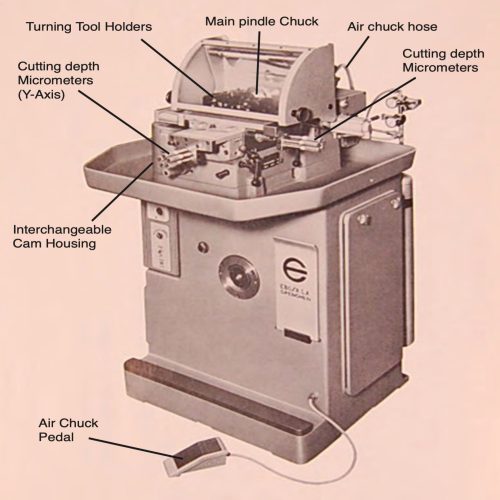
The Ebosa turning machine (left) is really an auto- mated lathe with its main chuck facing towards the operator instead of the usual left position of the chuck on the lathe. If you have experience using lathes, imagine standing at the left side of this machine, and the chuck would fall at your normal left, and the cutting tools would be on your right. This is a six-cycle automatic lathe ideal in machining lens barrels, and watch cases.
Ebosa works like a cam machine. To start with, a pedal operated air chuck secures the part to be machined. As the machine starts its cutting cycle on the part, a rotating cam pushes the X, and Y axis to their starting points. Translation of X, and Y axis are air operated, and their finish points are set by the six micrometers that are preadjusted for each X-Y cut. Up to six operations can be performed in preprogramed sequence at a relatively high speed. There are other machines that we’ll be visiting throughout this issue.
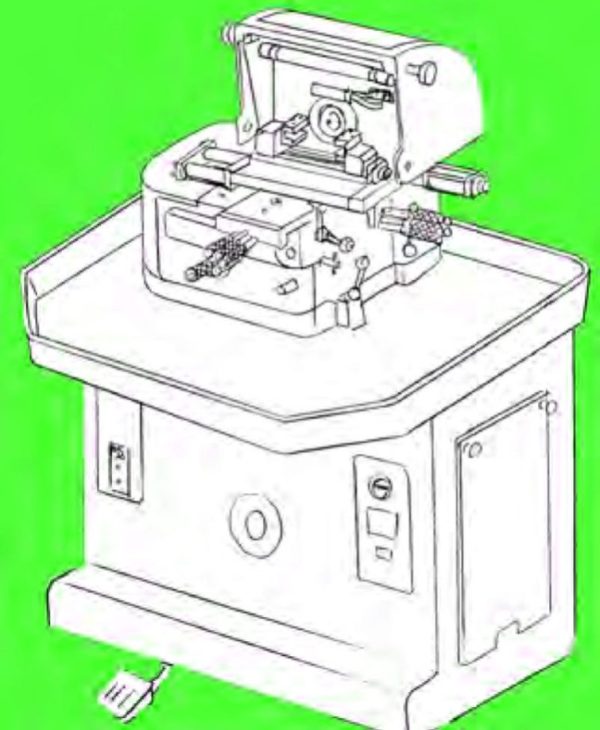
Eposa Lathe used in both watchmaking, and producing lens barrels.
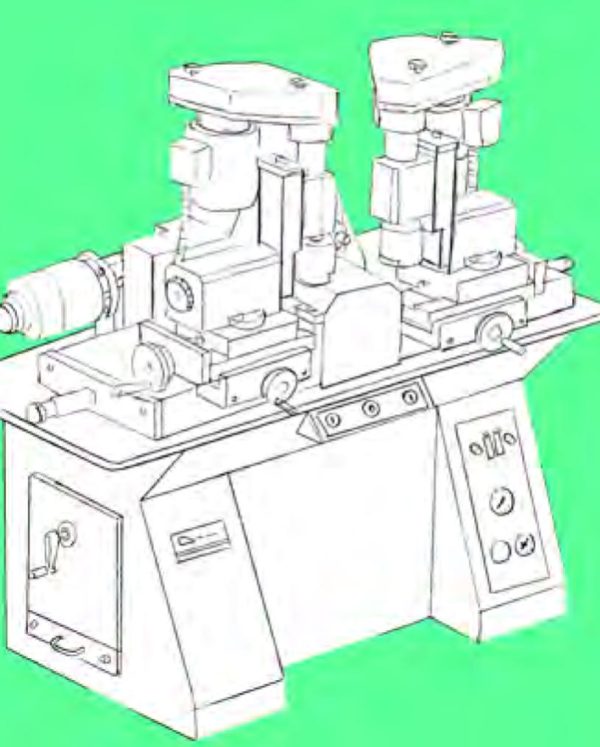
Bumotec S32 Replicating Machine produces watch cases from a sample
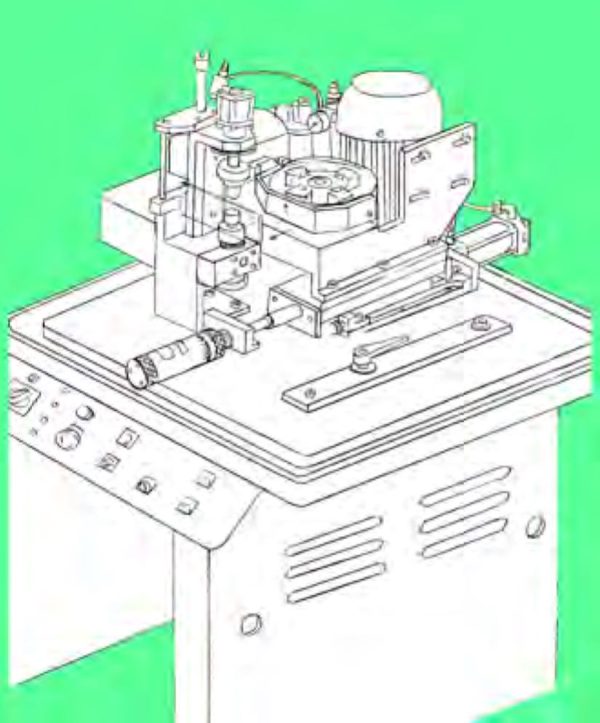
Bosha diamond wheel dial diameter cutting, and shaping machine
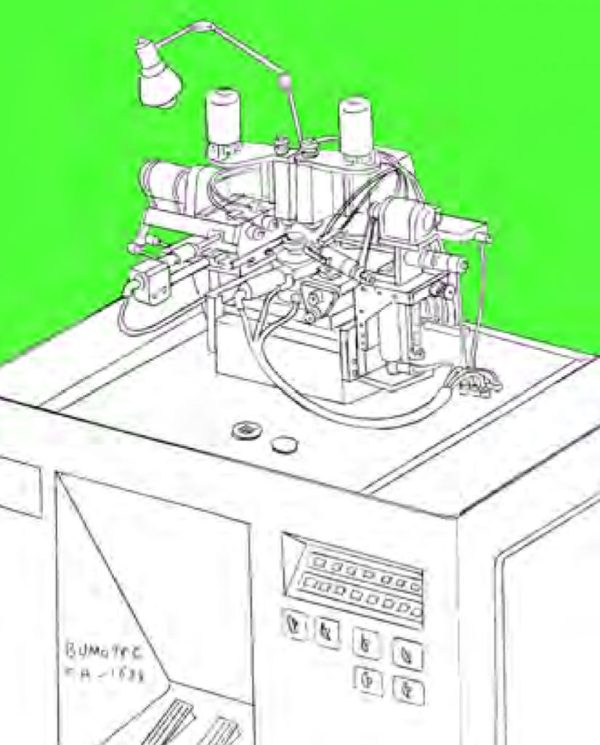
Jolia machine drilling the side holes on the watch case
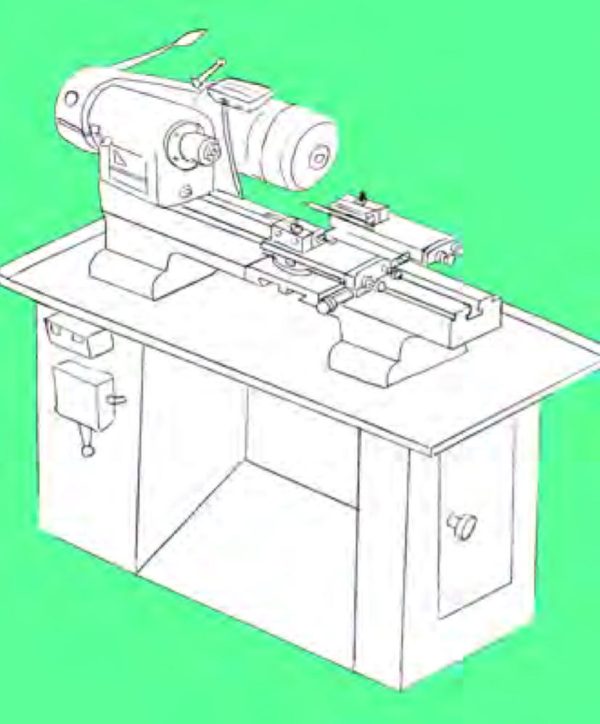
Schaubline Watchmaking Lathe for cutting watch cases
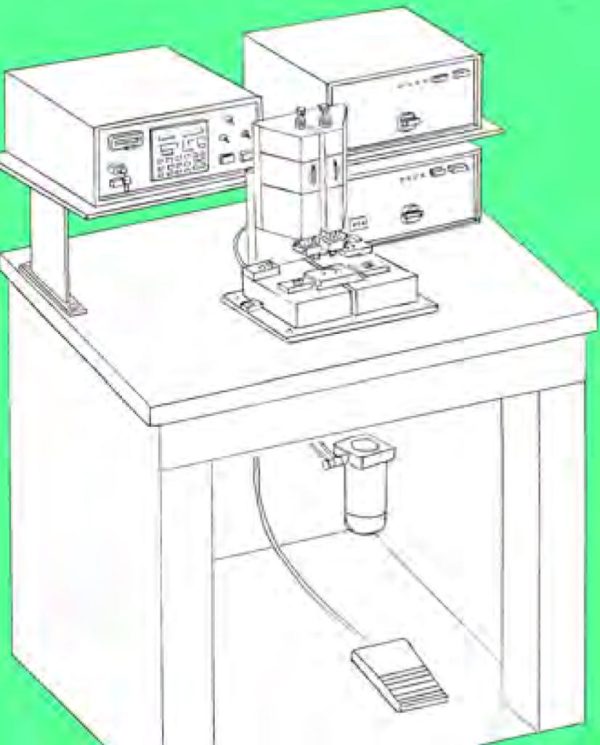
Covatec machine welds dial support pins on the back fo dials
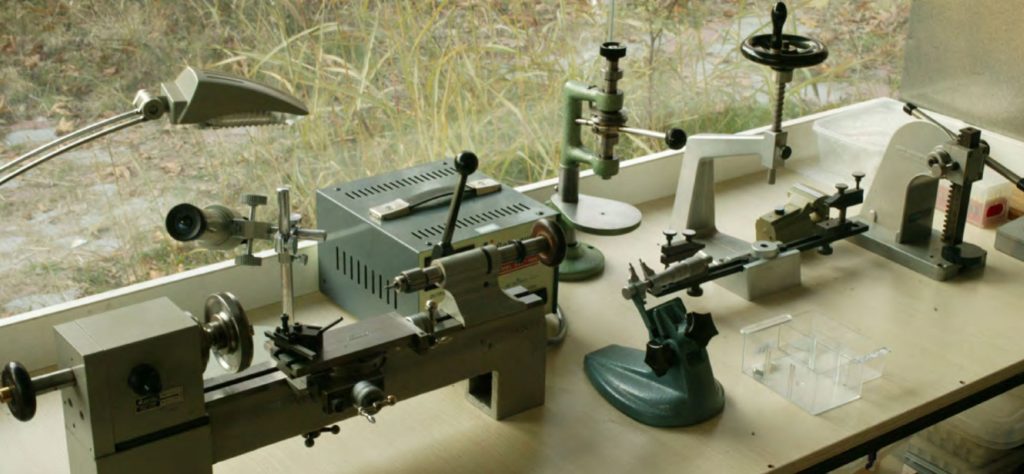
Levin 10 mm precision lathe, Bolova micrsocpe, Bergeon drill, Bergeon tapping and boring stand, and precision press.
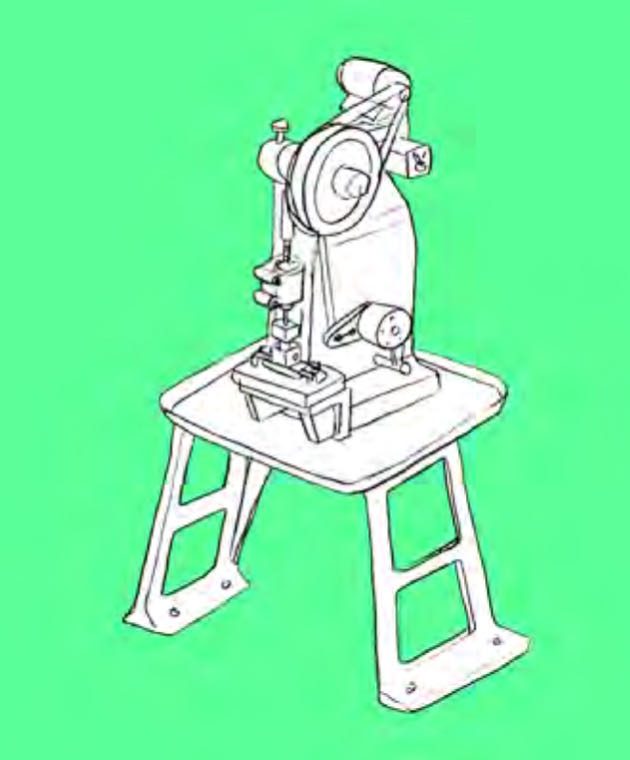
Wire punching macine to cut dial support legs from a roll of brass wire
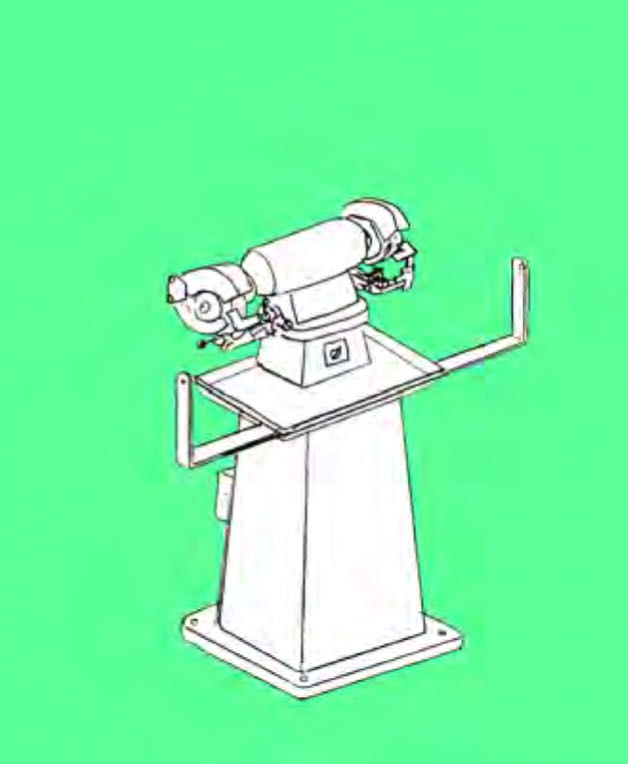
Tool grinder with precision tool guide stage, and angular adjustment
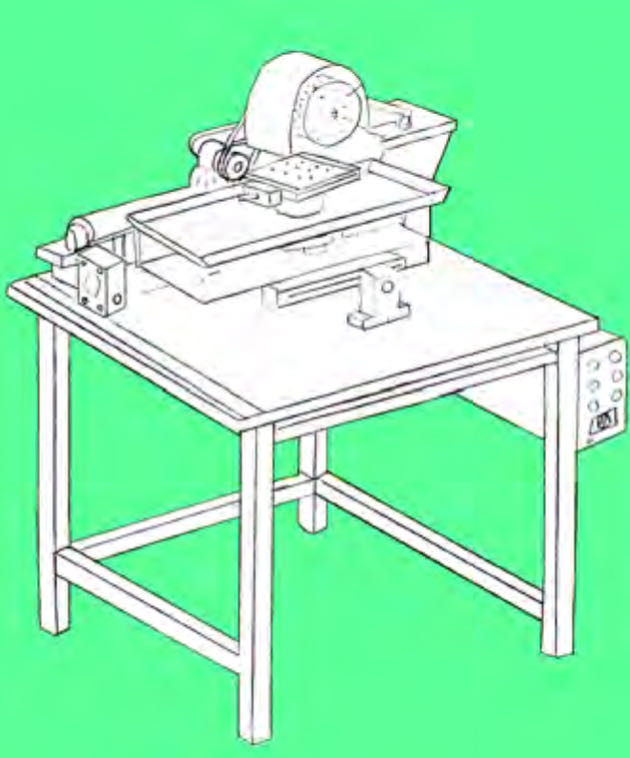
Firex dial polisher lays down paralell texture on the dial face
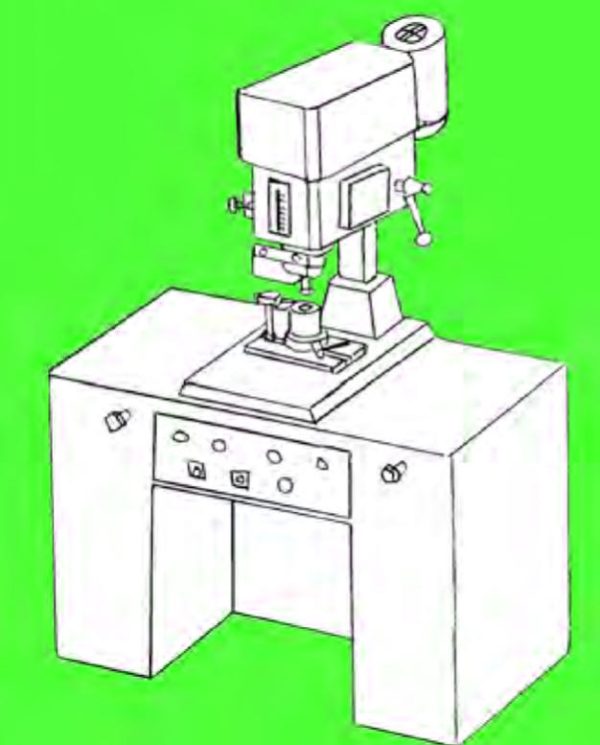
Bumotec S25 Back Cover Cutting Mill
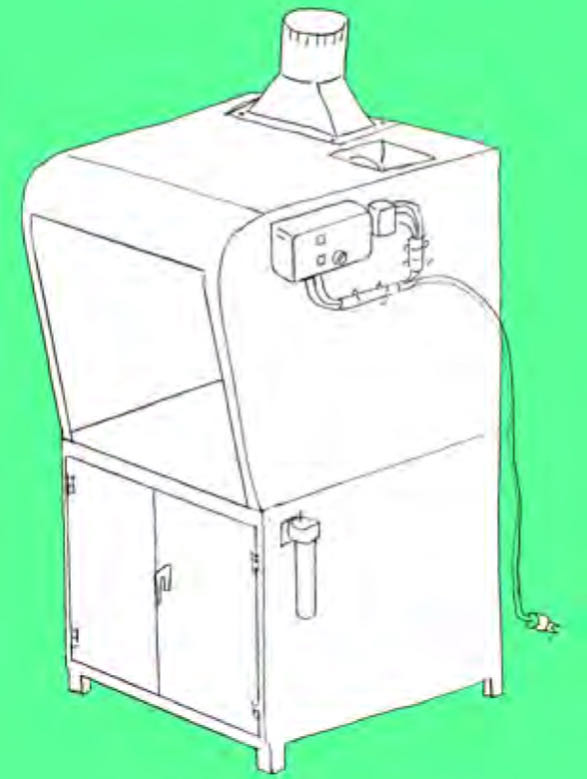
Painting Champer with Spray Gun, and convection fan

Dial paint drying oven with watch dial, and case trays
A wristwatch is made by assembling a number of parts together:
1) Watch Case
2) Movement (Quartz or Mechanical)
3) Watch Dial
4) The Crown
5) The Hands
6) Wrist Strap
7) Front Crystal Cover
8) Back Cover
9) Movement Centering Shell
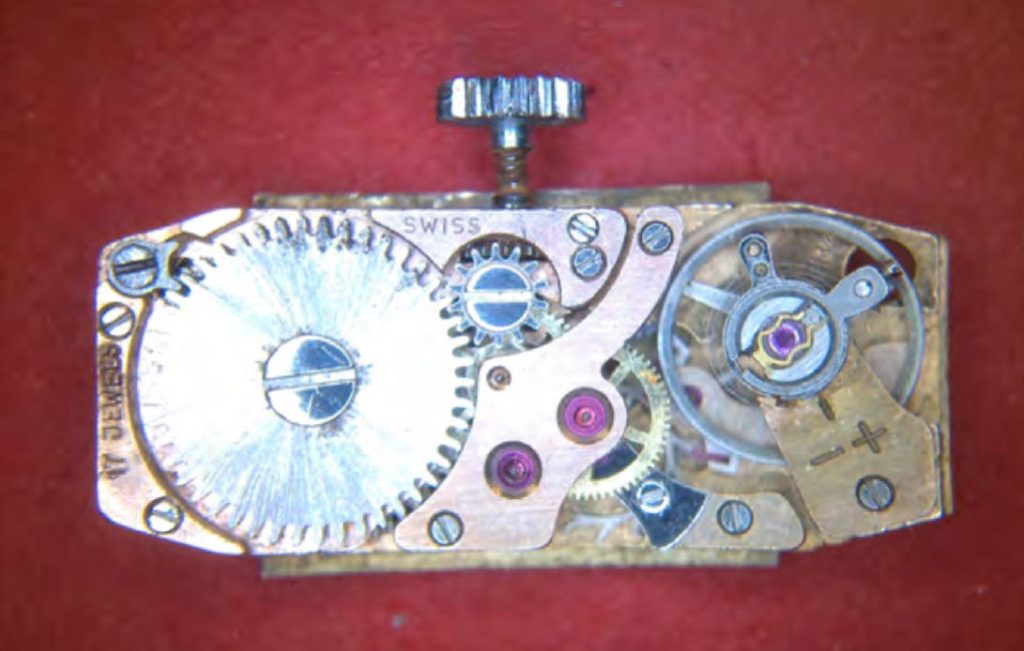
We’ll learn how to build a watch by visiting a small watchmaking factory. Some parts like the watch dial are created from scratch, where as other parts such as the movement are bought from other suppliers. One has to be passionate about the art of watchmaking, and have a great deal of devotion to build good quality watches.
The wrist watch is part of what is generally known as micro-mechanics. Watchmaking is engineering at its best because it deals with general public as much as the mobile Phone. While It is engineered for perfection, it also has fashion in it, as well as many of the arts. One could get lost inside a watch as one would get lost in a recreation park or carnival. You don’t need a guide while wondering inside a watch. The mechanical watch will teach you on its own how to treat it with respect. You’d learn how to be gentle with it once you see the delicacy of its making. Poets show their love through poetry, while watch makers show their love with micromechanics. If you are a watch expert, you’d pay for the love that is put into making it. This installment is just an entry level display of the art, and the precision tools it uses to achieve it.
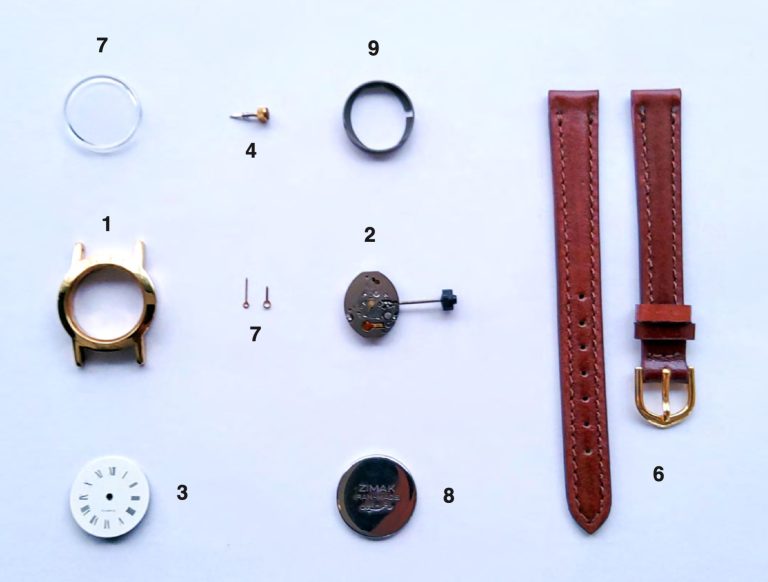
1 The Case
Watches are picked for their outer appearance, namely, their casing. Watch cases usually range from 7 to 9 mm in thickness.
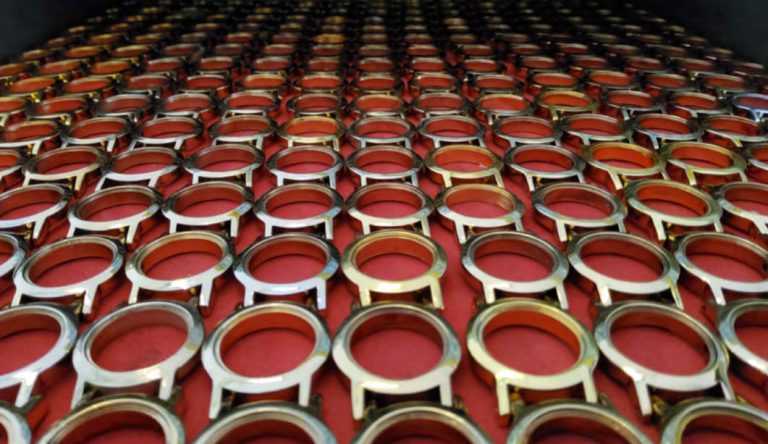
You could produce watches today without owning a factory: Pick parts from catalogs, containing a full range of pre-made cases, movements, dial faces, watch hands, crowns, wrist straps, all the 10 pieces. There are companies all over Europe who do nothing but making them. They are so specialized in what they do that almost every famous brand relies on them, including Rolex, Omega, and many luxury watch companies like Cartier. So why build your own parts?
For starters, this might be an appealing option but not for people with taste. You can’t have your own unique look if you keep building your brand from off the shelf parts. Most watch manufacturers won’t make their own movements but, in most part, many parts are built in house. As we follow the process of watchmaking in this small shop, we’ll see how this shop cares about details of their watches.
Designing the watch case is not that trivial either. There are several types of watch case styles, and the most creative watch designs are not fully water resistant. Water proofing a watch puts so much constraint on its design. The 100 m waterproof Rolexes look more like a submarine! It’s still beautiful because so much thought has been put into designing it. In its components, Rolex design is like a Hasselblad. It has design accents that are picked to give it its unique look. The bevel in Rolex is like the shutter speed dial on Hasselblad. It’s definitely not a Dieter Rams (less is more) design.
Going back to case design, the simplest watch cases rely on the dial to hold the movement, especially when it comes to Quartz movement that only weighs less than as six times the weight of its battery. Th crown that sets the watch is drilled just beneath dial’s seating plane as shown in this side view illustration. There is one detail in watch case manufacturing that only a few notices: How is the wrist strap securing bores are drilled from the inside, not outside of its lugs? This is a specialized operation that is performed by Julia drilling machine. It’s among the most complex machines that was dis- tributed by a Swiss firm named Bumotec.
Julia is a pneumatic drilling machine (opposite page) that fabricates all the side bores on a watch case before it goes to polishing. It could perform up to six drilling operations on the watch case; Two from above, and four on the sides. The machine could be programmed to work automatically. The inner bores on the lugs are drilled by a combination of two side drills, and four rotation angles.
The next step is polishing the case, and metal plating to make the watch case more sweat resistant, and also scratch resistant. For Gold coating, the watch case also receives a thin plastic coating to protect the gold from hand sweat. With proper coating a watch case could maintain its finish for 5-10 years (refer to page 30).
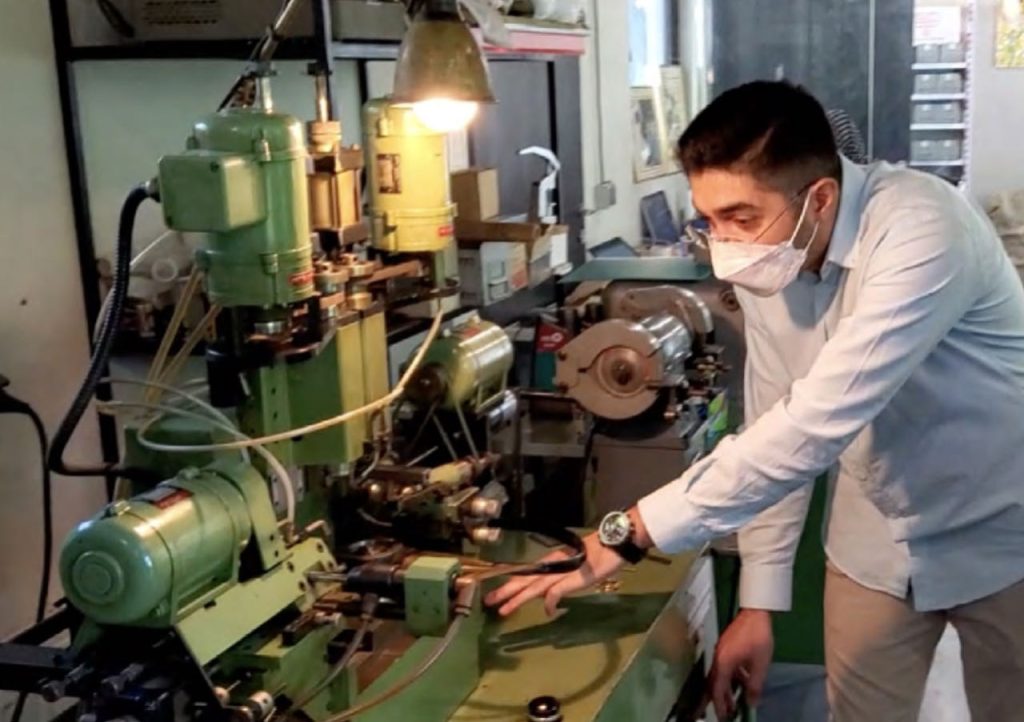
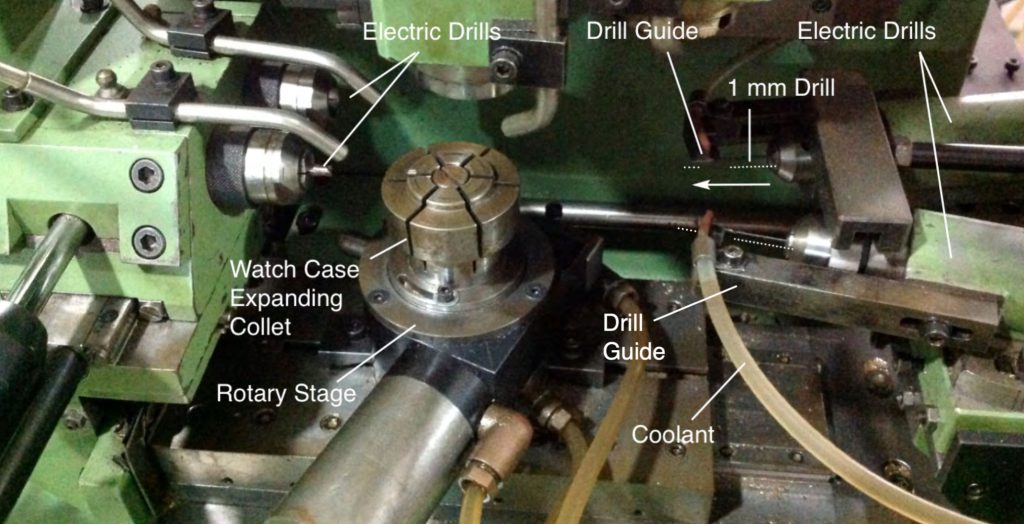
Mass producing watch cases requires precision side drilling done mostly by Julia drilling machine (above). This pneumatic multi drill Swiss machine makes all the side bores in watch cases. The 1 mm blind holes are made from inside the strap lugs. This takes place at a slant angle with super long drills for clearance. Swiss ingenuity uses L shaped drill guides close to the drill tip for precise drilling. The drill guide drops in between the logs to perform the drilling operation, and is lifted up to allow the watch case to rotate to its next side or top drilling position. Winding stem bore is drilled by larger drill heads on the left. All drilling angles are fine adjusted by graduated micrometers, and fine screw dials.
2 The Movement
The movement is the most outsourced part of the watch, yet it’s always considered to be uniquely manufactured in house.
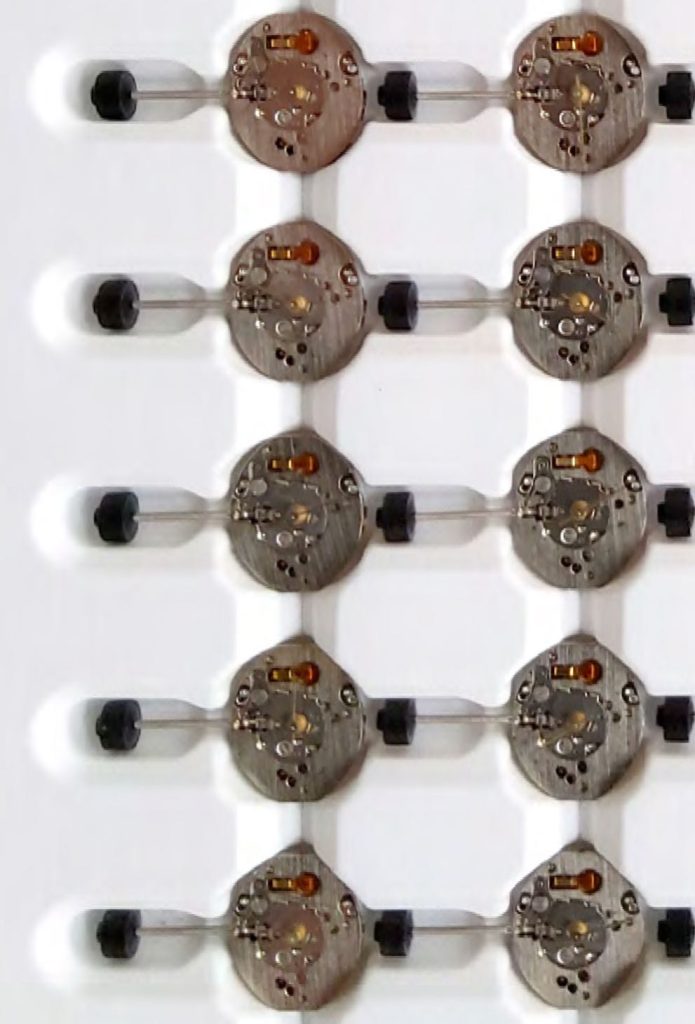
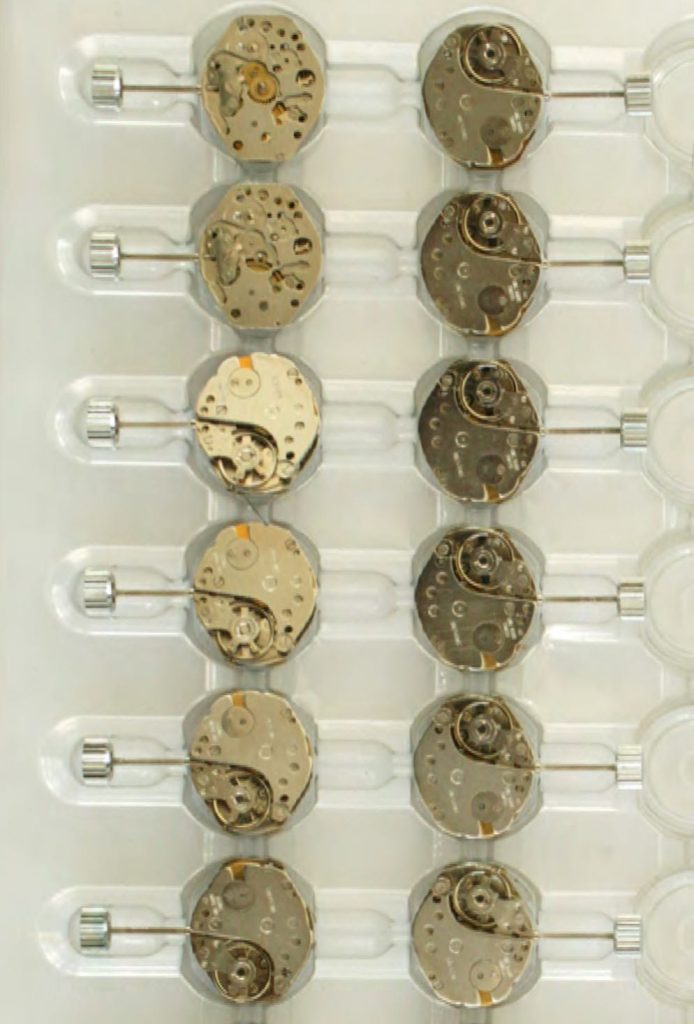
Quartz versus mechanical: Although I personally like mechanical movement (right), quartz is so easy to assemble, and maintain. The mechanical watch drifts with temperature, and by its angular orientation. If you watch the mechanical es- capement under an electron microscope, you’ll see the friction reality facing micro-mechanics. As the angle changes, so does the friction. Breguet, developed the Tourbillion watch to average the friction to some extent. In most part, we’ll follow the quartz watch in this small factory. A section at the end will cover maintenance of mechanical watches.
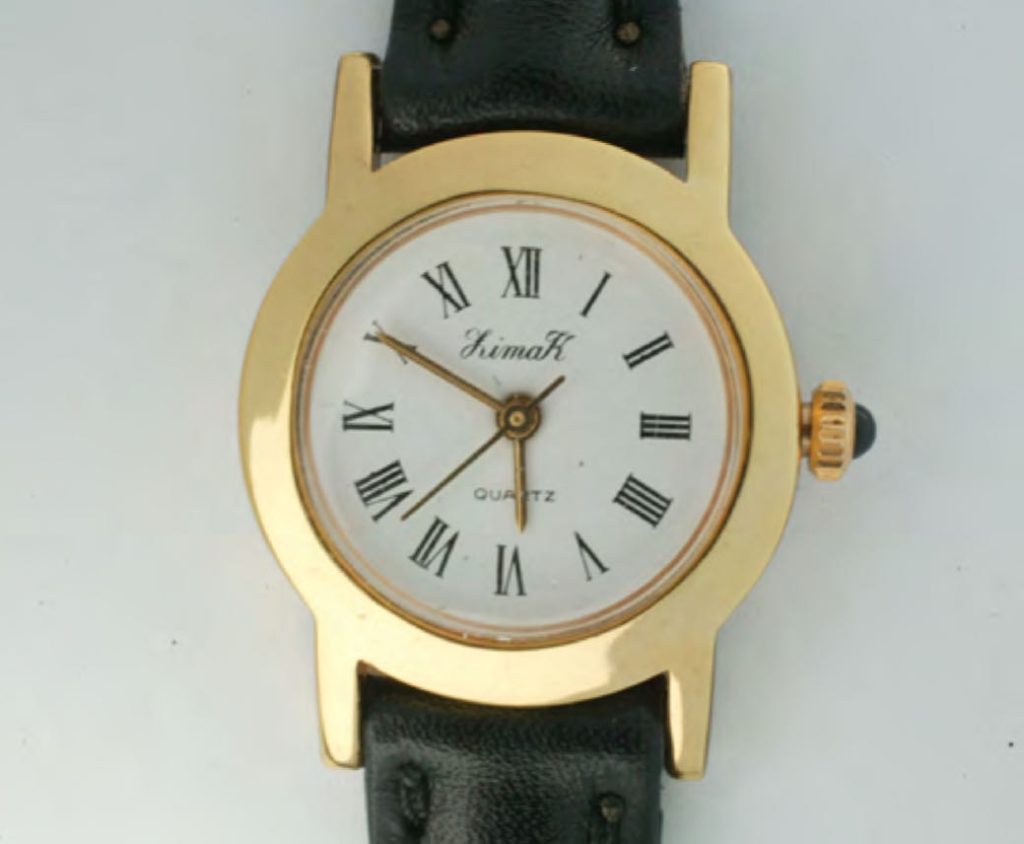
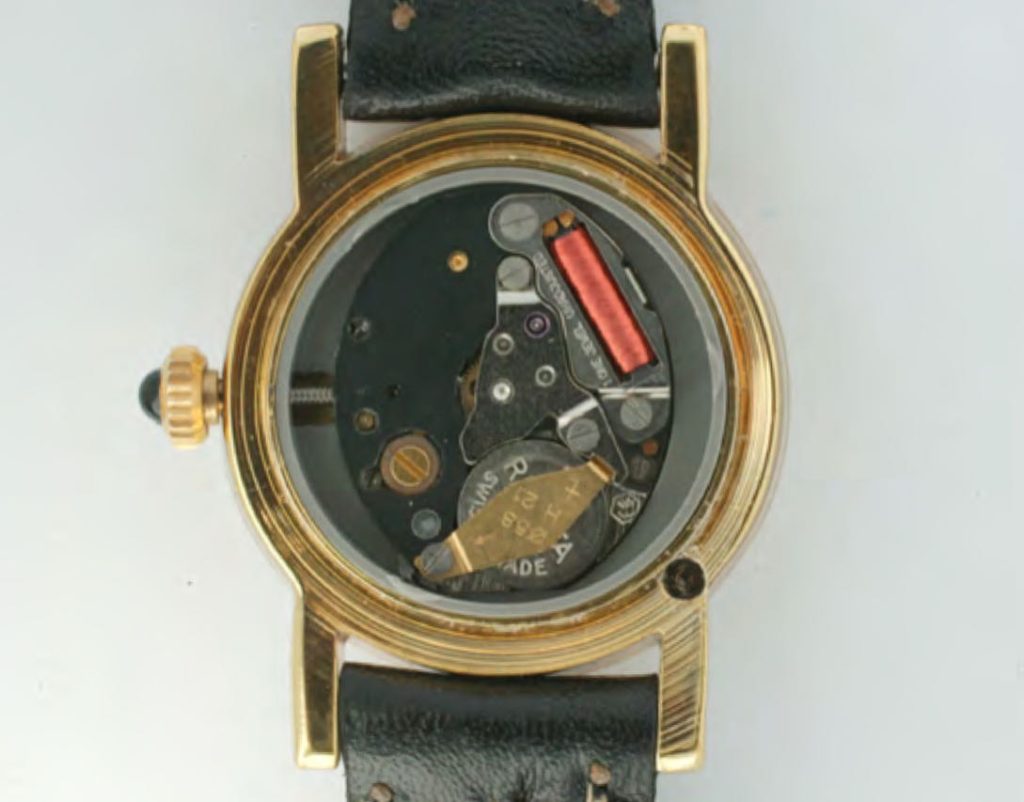
A ladies watch, product of Zimak watch factory (left). The back cover is removed for battery replacement (right).
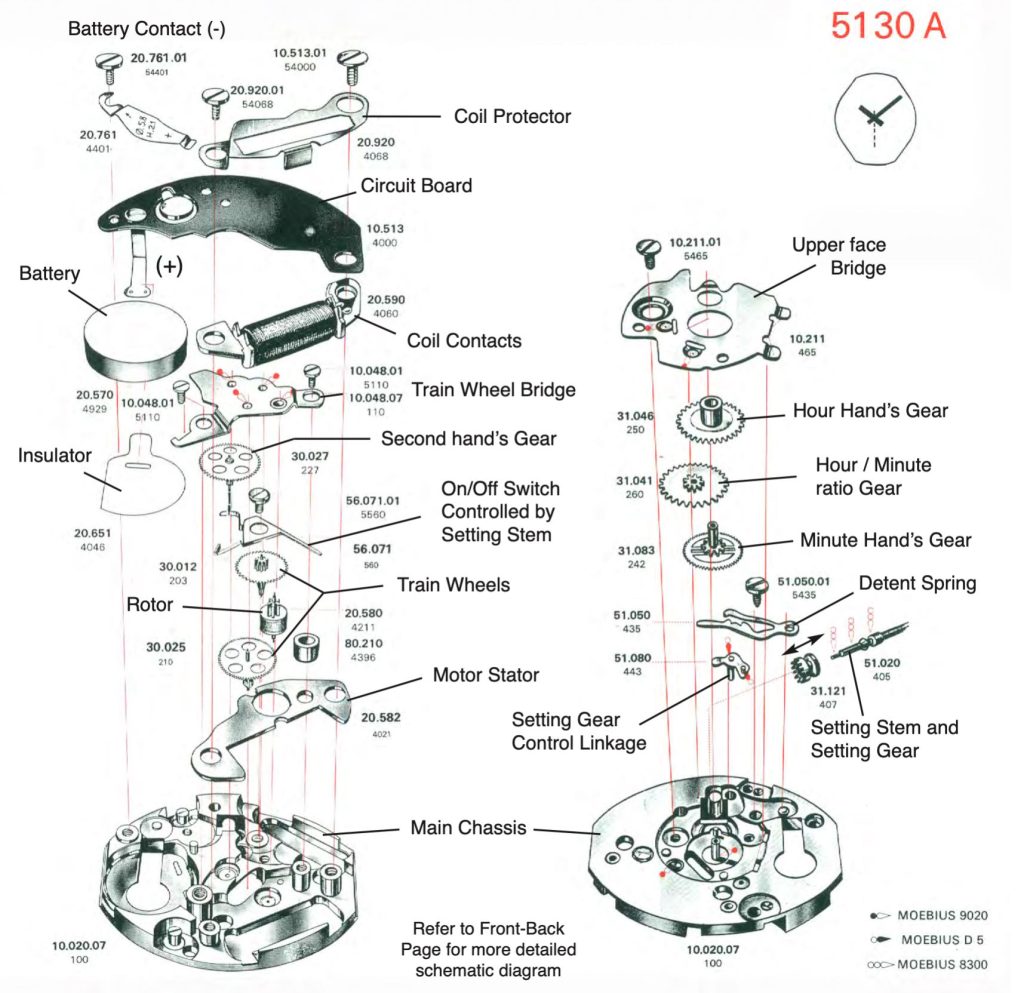
Exploded view of Caliber 5130A Quartz movement (above) revealing its main motor coil, electronics board, and its drive gears.
Right, troubleshooting, and testing the 5130A Quartz movement could be fully performed using an oscilloscope, and a standard voltmeter. The condition of the coil (above) is verified using an ohmmeter by touching the probes on its contacts.
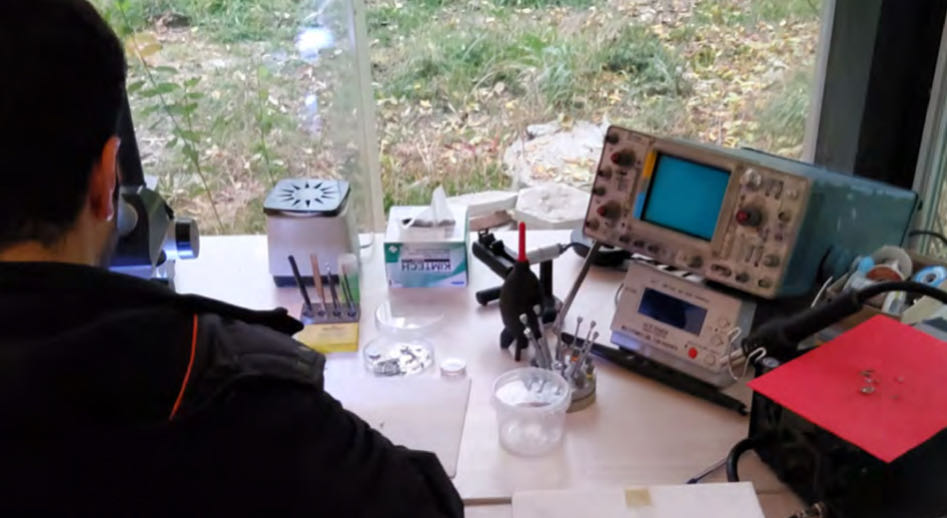
3 The Dial
The watch dial is the most invested piece of the watch. It is decorated to shine bearing the name of the watch.
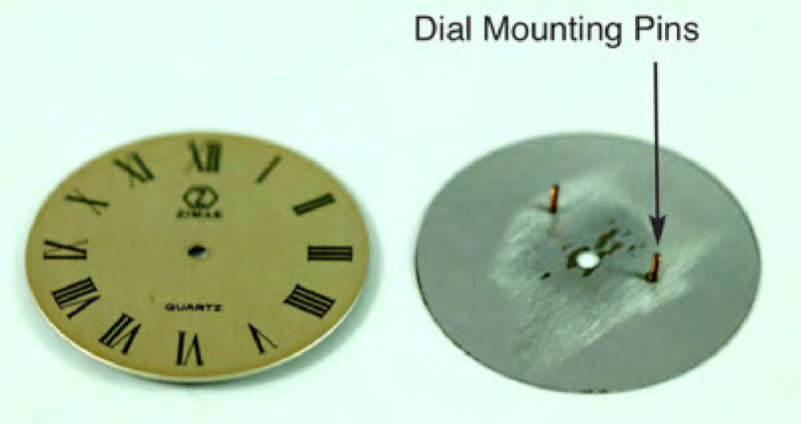
Everything is mechanically mounted inside a watch. Nothing is glued. Using high amperes, Covatec welding machine (right) welds these tiny brass legs behind each dial.
Dial mounting pins that are welded behind the watch dial are inserted in two openings around the watch movement and secured in place by set screws.
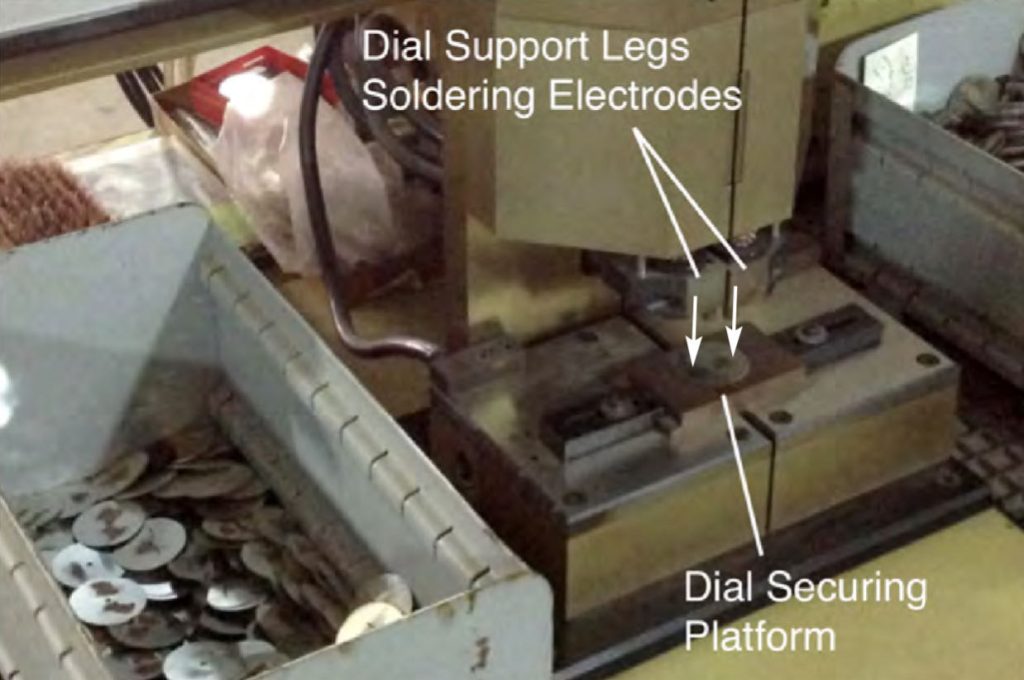
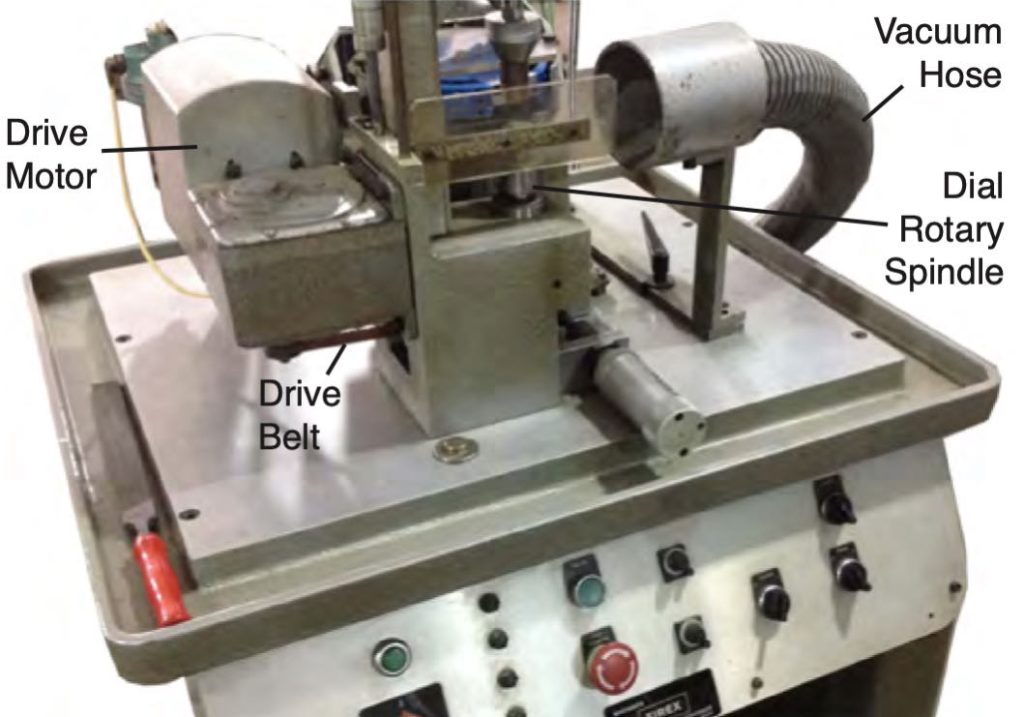
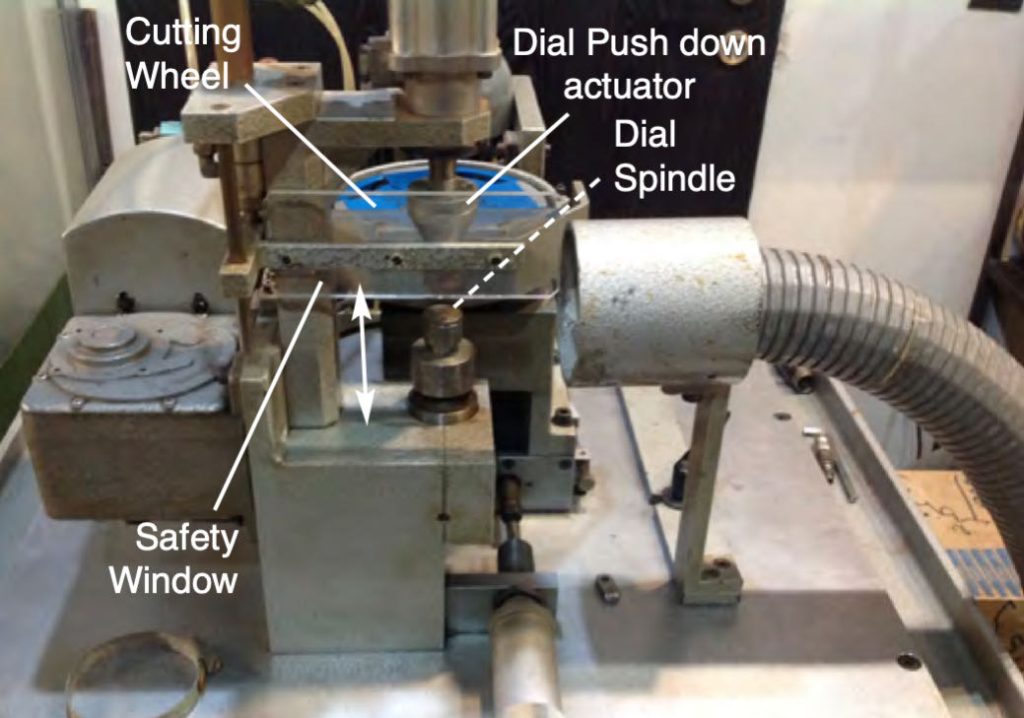
The watch dial diameter, and inner diameter of the case have a close fit. The watch dial cutting machine by Firex cuts it to size plus generating various shape dials from a template mounted below its spindle. The cutting operation is done automatically by rotating the dial 360°. The vacuum hose on the right guides the micro cut particles to a waste chamber. The huge micrometer in front adjusts the cutting diameter of the dial. The spinning wheel has diamond blades.
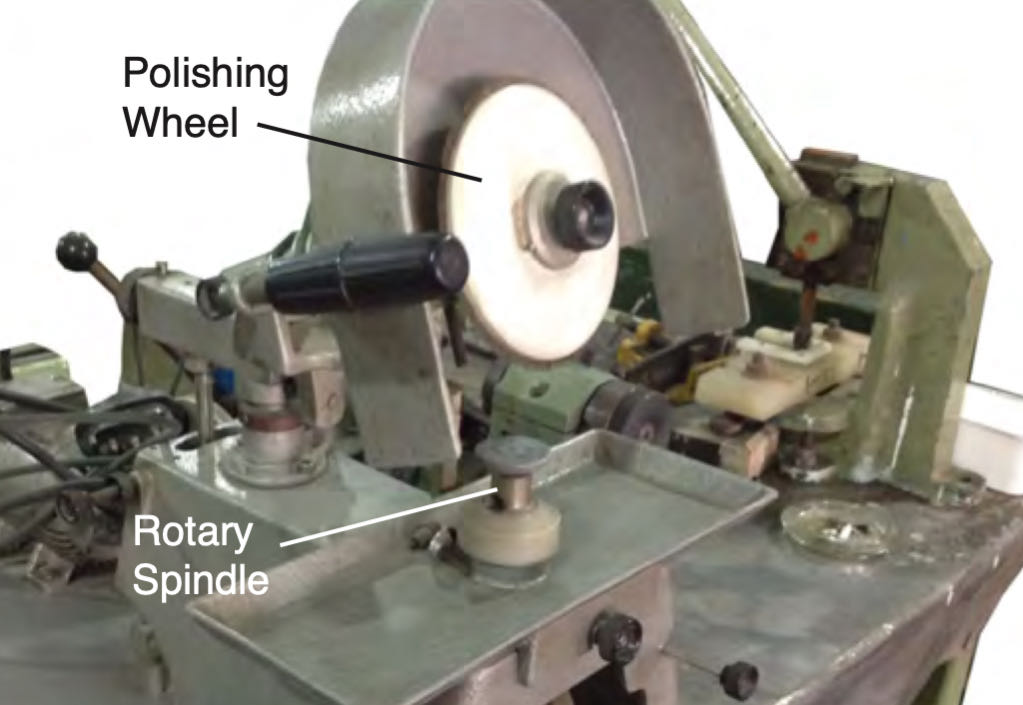
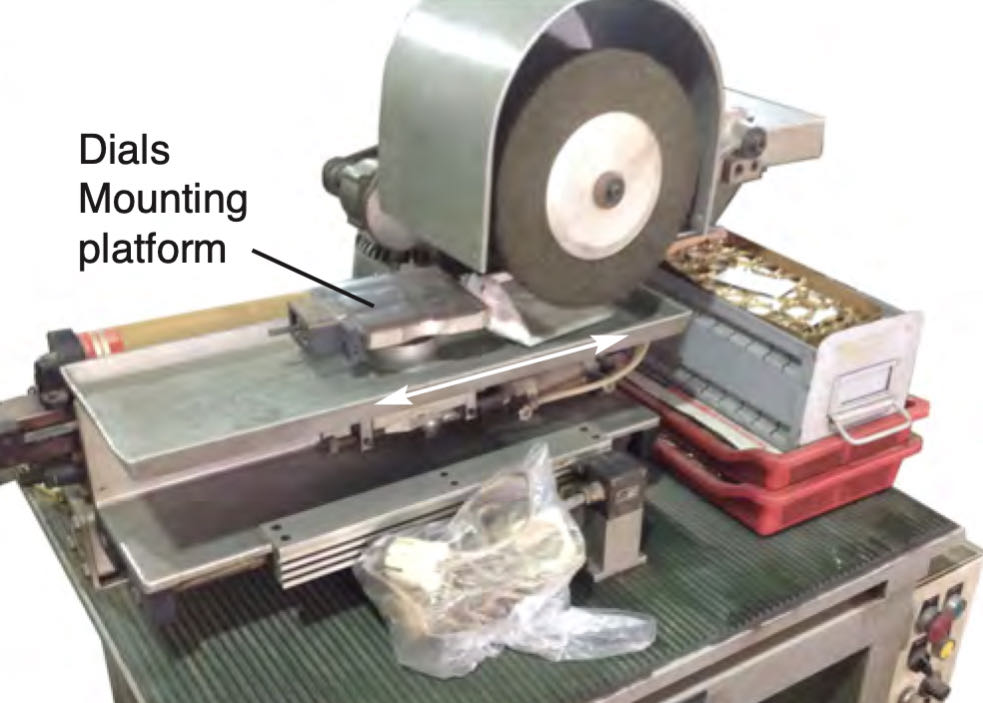
Two Firex dial polishers lay down paralell texture (right) or sun-like rays extending from the center of the dial (left).
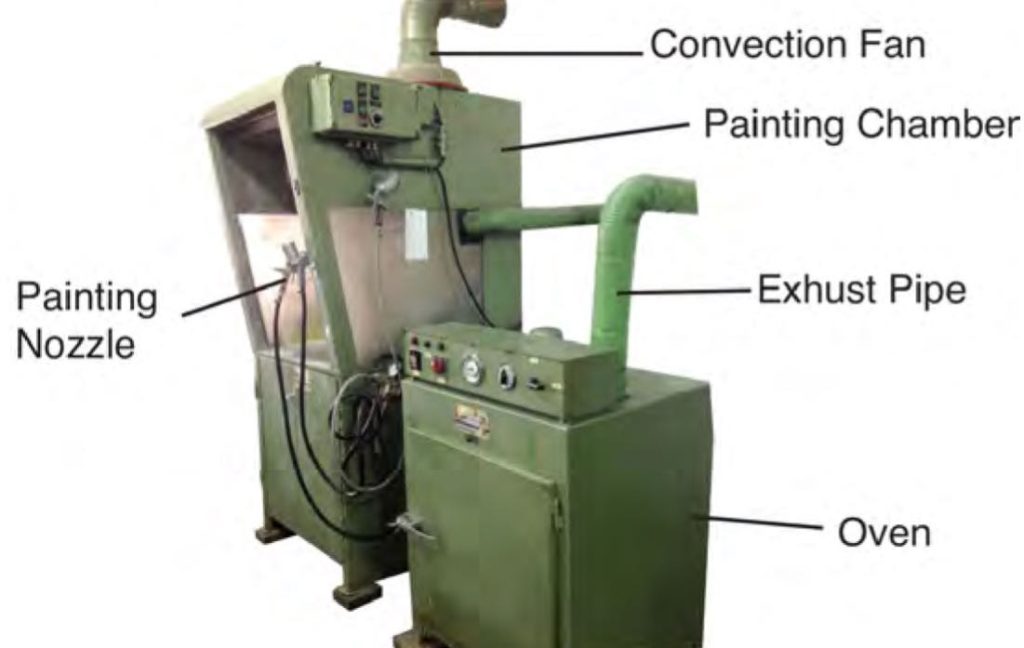
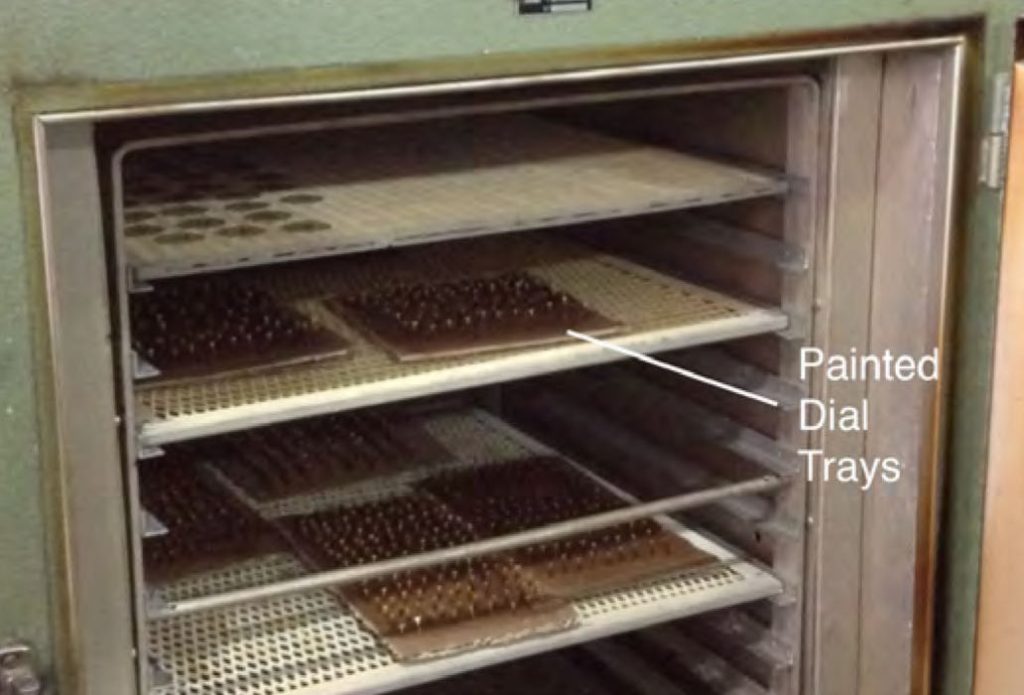
The spray paint chamber for dial face (left), and the baking chamber (right) coats the brass dials to desired colors. The Baking process produces a hard paint that won’t be wiped off with alcohol cleaning. This is a compact / precision painting chamber that provides precise control of face dial painting. After the first layers of primer, and the cover paint, and baking process, the dial is ready to receive its precise graduations applied by a stamping machine (below). The dial is returned to the baking chamber for its final hardening.
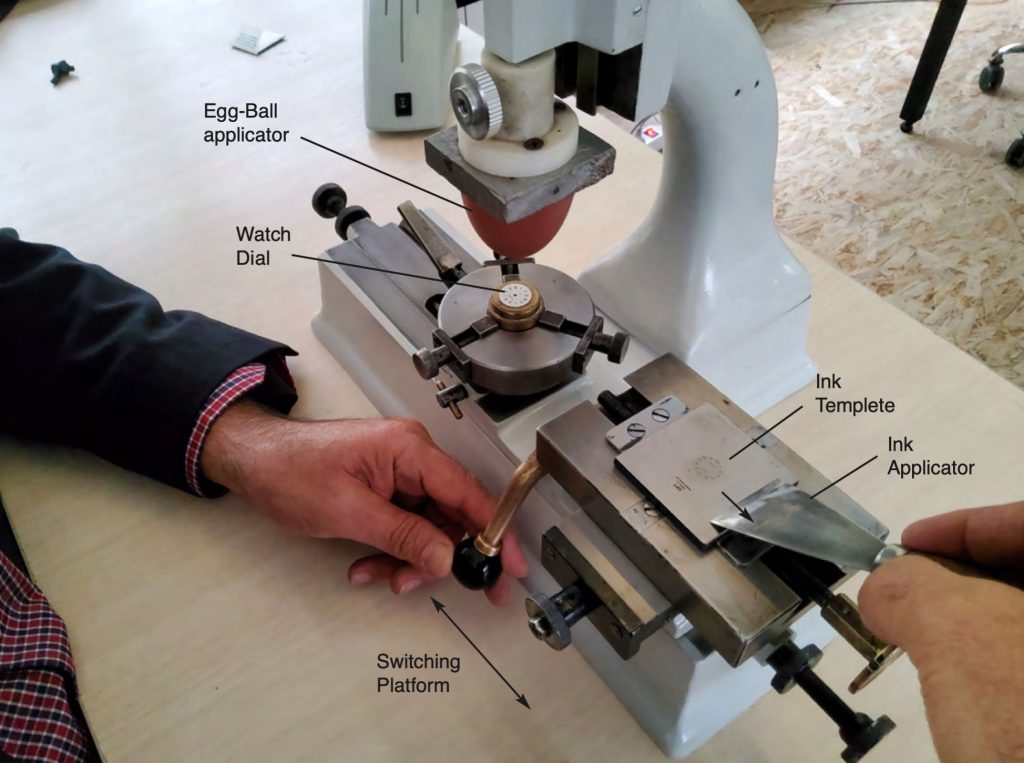
Roger Ferner dial stamping machine uses templates (right) to imprint precise marks on the dial face (left). Applying the ink on the template (right), leaves off the dial marking ink on the etched template. The ink pattern is lifted off with the soft egg ball applicator, and imprinted on the dial face. The angle of watch dial in the stamping machine (above), and the po- sition of support legs welded behind each dial by Covatec machine (opposite page) must be in perfect alignment. This becomes so crucial when stamping watch dials with a calendar window.
4 The Crown
The crown is the user interface from outer diameter to the inner watch movement to set the time.
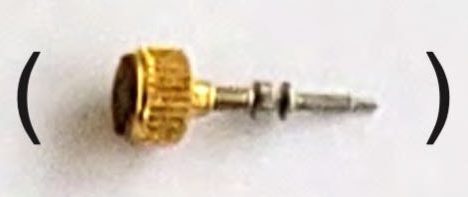
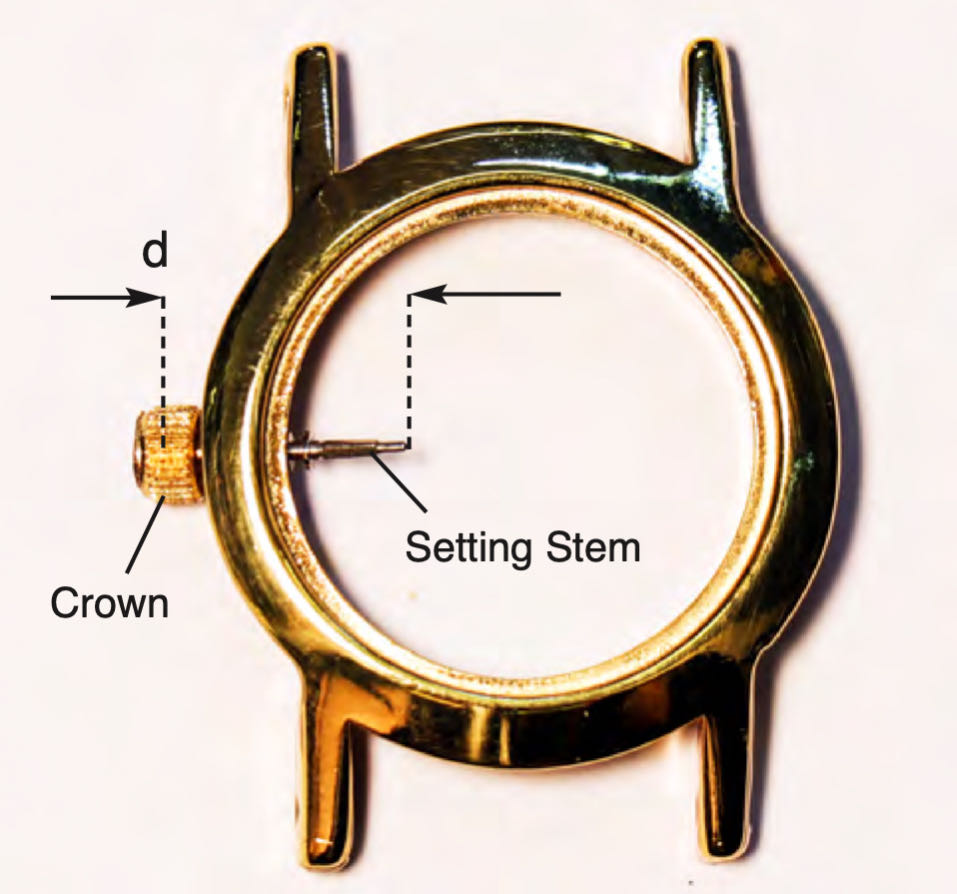
Attaching the setting stem to a watch seems to be trivial but it’s not. Watch movements are supplied with a default length setting stem (page 10), and a plastic crown that needs to be cut to length depending which case size you are going to use. The watchmaker buys the crown separately to replace the dummy plastic piece. Shortening the supplied stem, for its insertion into the watch requires specialized tooling. This operation requires exact cutting length (d), and the screw tip needs to be deburred, and epoxied inside the crown.
The Seiler machine (below) is designed to do just that. It uti- lizes a diamond powder cut off wheel to cut the stem to length while it is precisely held in place by an 8 mm collet. The shortened stem’s tip also gets conically deburred by a step built into the cut off wheel as the push-in arm is further moved in to its stop (opposite page). There is a crown se- curing collet on its opposite side (below) that drives the crown onto the shortened stem after the cut-off operation, and stops automatically by a micro switch as soon as the screw reaches the end of crown’s blind hole.
To really appreciate this, try using Dremel to cut the setting stem. You’ll be spending an hour to fit each pin.
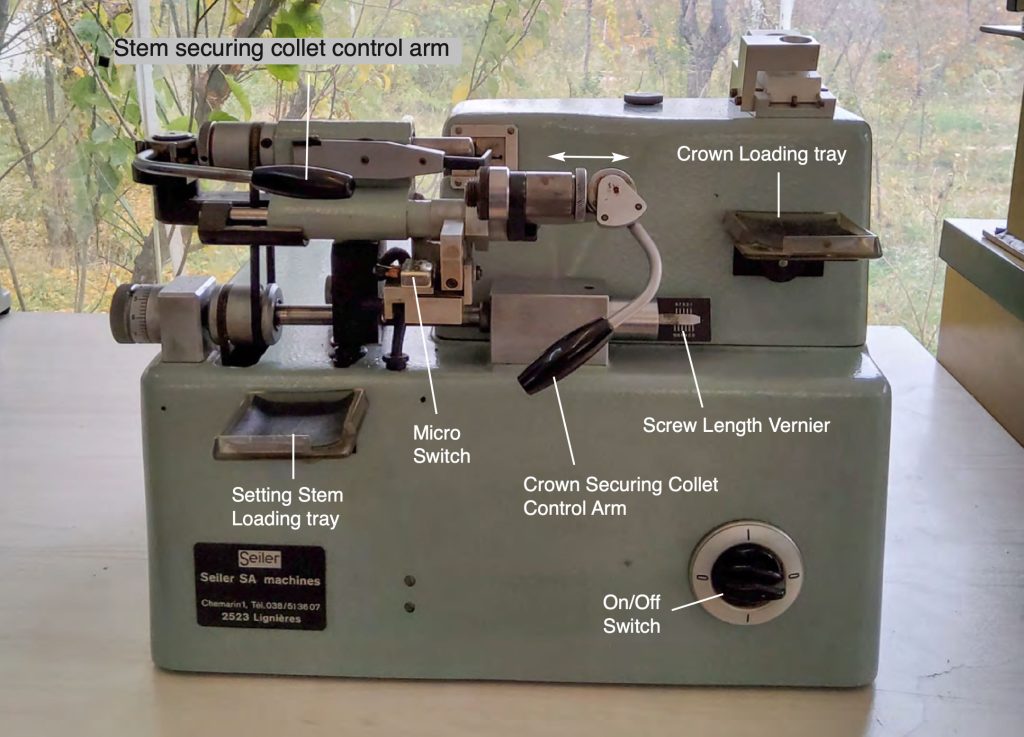
Seiler stem cutting machine
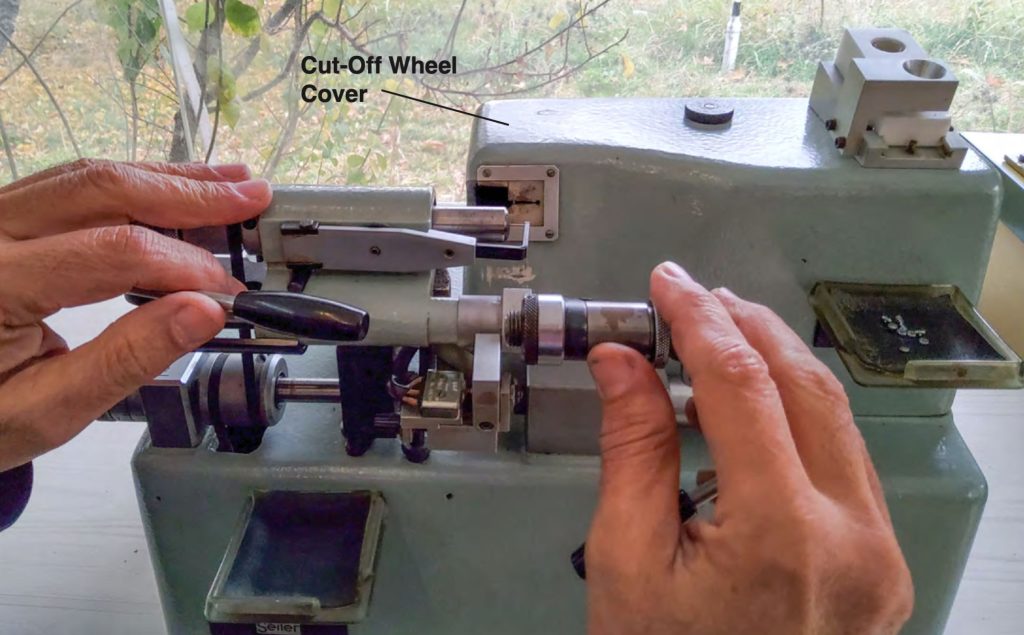
Cutting off the setting stem to length, and installing the crown is done precisely with this machine.
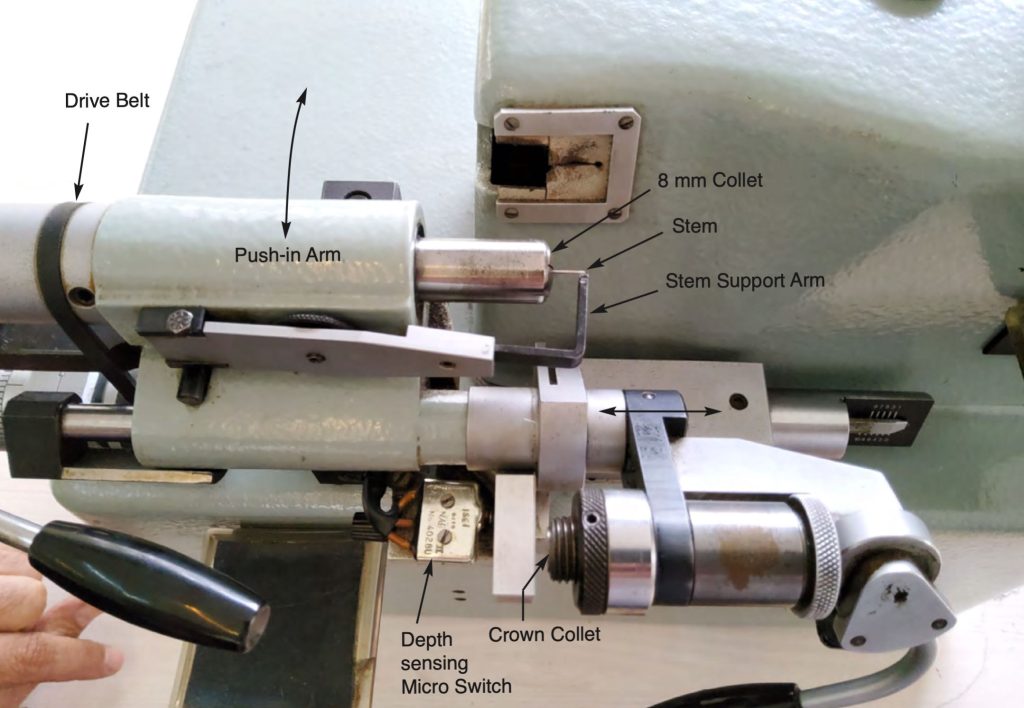
5 The Hands
The hands are the main means to tell time but also if designed properly, the least noticed part of the watch.
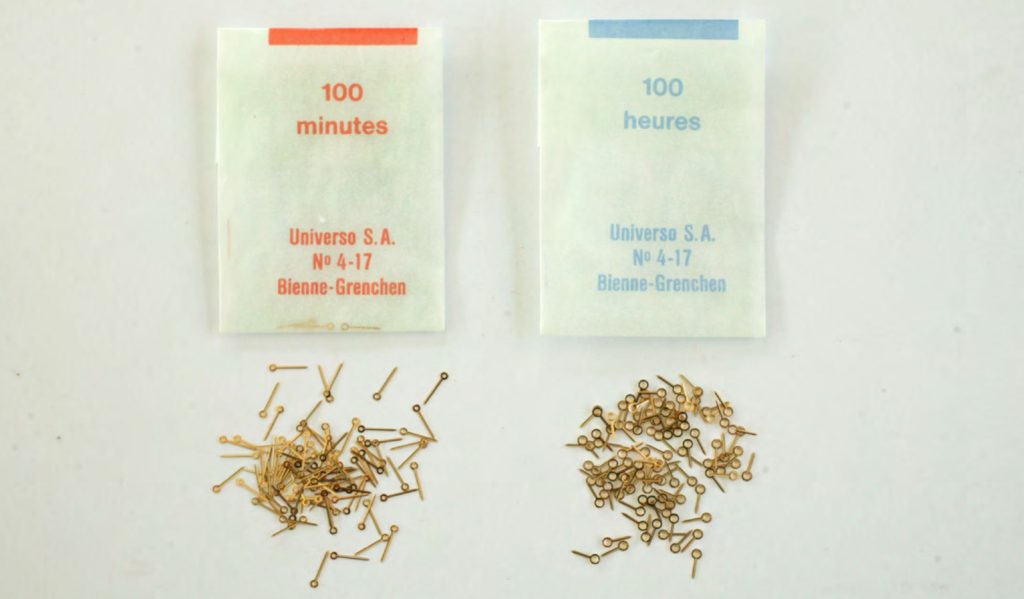
Hands fitting tool is the standard way for installing watch hands on a movement. This tool utilizes centering supports to center a variety of movement calibers on its mounting platform. Most of these centering supports are available by watch tool suppliers like Bergeon, but it is also the most common fixtures produced in the tooling department.
Movement supports (below), cannot be so tightly designed to fit onto the hands setting tool. The technician has to be able to use the hands fitting tool with moderate comfort, and not be irritated with its constant lockdown. So there has to be acceptable mechanical play into this device. At Lange Sohne, I have seen experienced watchmakers using a flat mounting platform (with no centering) for fitting hands on their chronometer watch movements. For that, they could only look and feel the centration of the push-down rods with their hands. In either case, fitting the second hands are really challenging on a movement, considering the center pin to hold the second hand measures only 0.1 mm (opposite page). This is the most vulnerable part of the watch, second to the balance wheel, and the pallet.
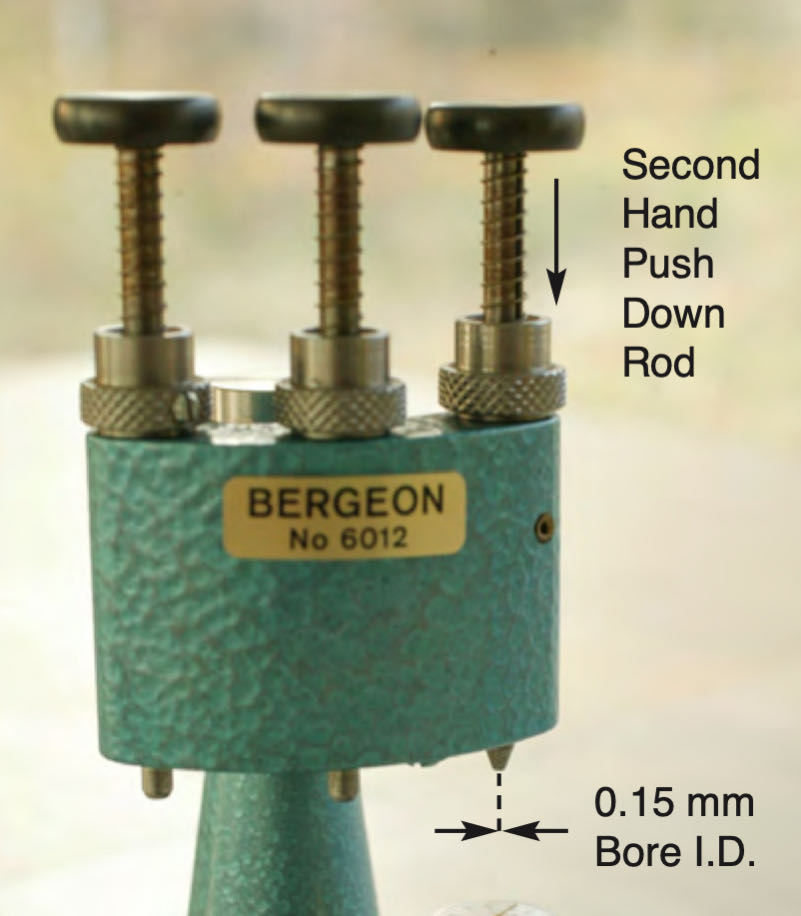
Hands fitting tool for installing watch hands
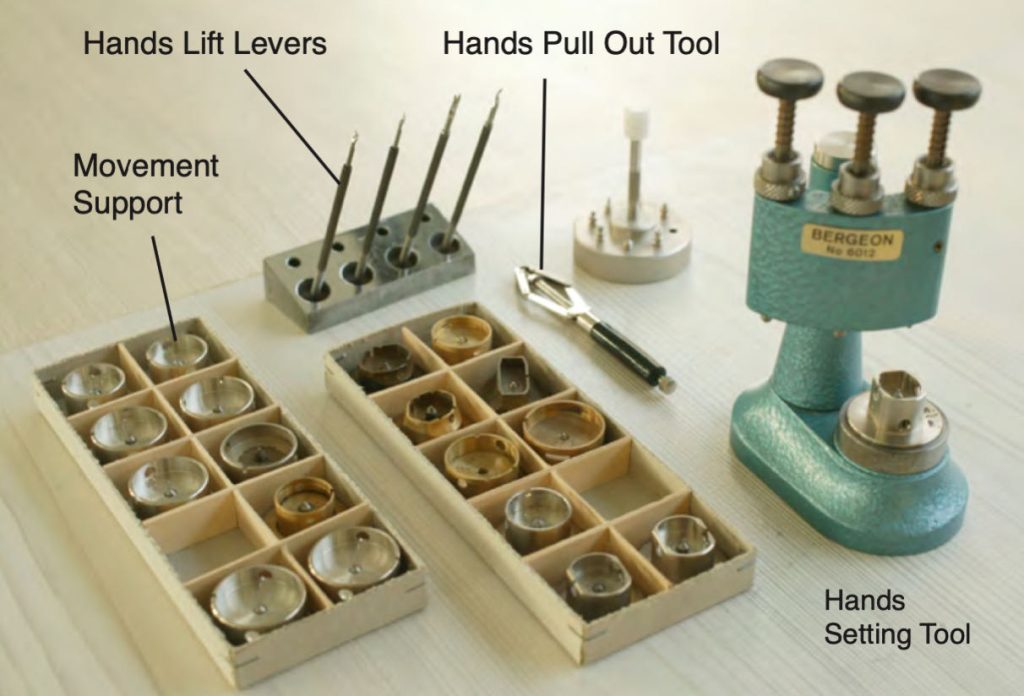
Specific mounting supports to fit each and every movement
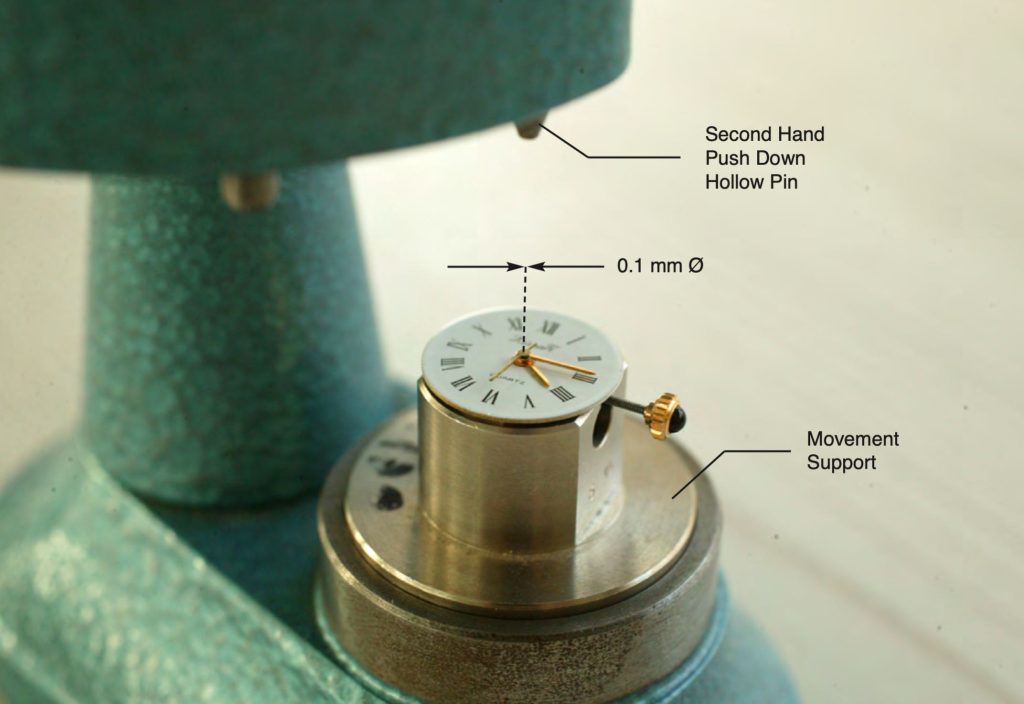
Fitting the watch hands in their 1.5 mm space above the watch dial (below) is an intricate task performed with specialized tools under a magnifier or microscope. Never attempt to install the second hand without proper tooling.
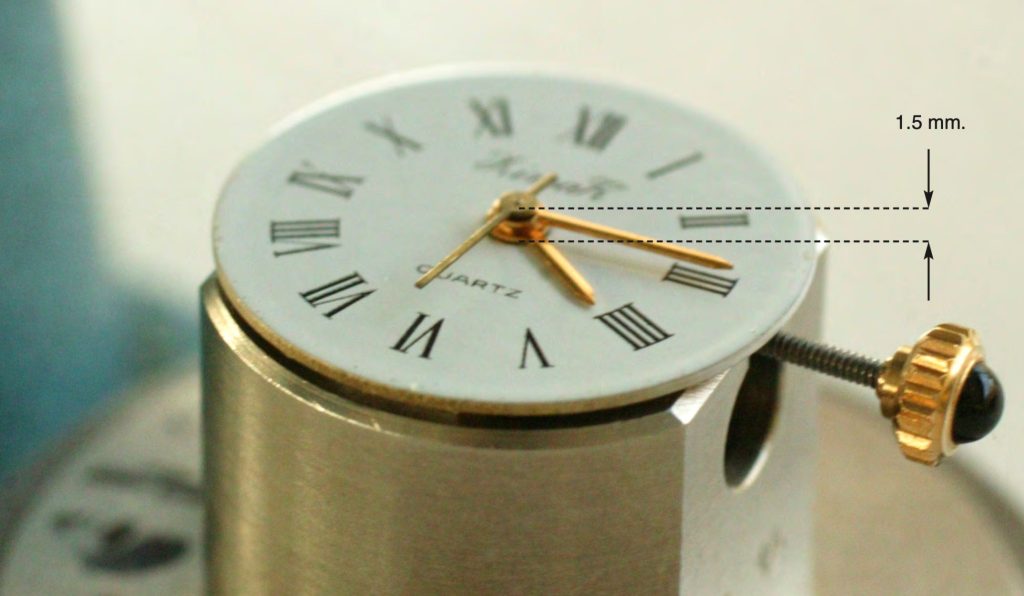
In hands setting, it is necessary to set the time so both the hour, and minute hands will line up at 12 o’clock. If the dial print is exact, the rest of the hours, and minutes will fall right into place. Calendar watch hand setting is more involved.
6 Wrist Strap
The wrist strap is the every day means to put on and off the watch. It is the most pronounced visible part of the watch.
In watches, the rotary path of watch hands would tend to make the watch case circular, and the band going around the wrist would tend to make it rectangular. In watch design, these two forms have been combined to reach the accepted wrist watch form (below, A). I personally prefer the rectangular case (B) because it brings harmony between the two forms. In mechanical watches, the rectangular movement is also my favorite design compared to the standard circular mechanisms.
Wristbands are more difficult to implement than they are taken by consumers. It involves both the case size, and the wrist size of the person wearing it. In watch design, the strap size is usually half the diameter of the case. The watch would look out of proportion when the strap size is too large or too small (A, C). When you order watches, you’d also have to specify your wrist size.
If your wrist size is 6 to 7 inches, a 38 to 42 mm case size is recommended. If your wrist circumfer- ence is between 7 to 8 inches, a 44 to 46 mm case is recommended. The length of the wrist bands for each case size would differ accordingly. I am not so much in favor of metal watch bands but in general, the length of wrist bands ranges from small (< 34 mm) to standard (39-42 mm), to large (43-46 mm).
Inserting the wrist band into the lugs have to be done professionally, leaving no marks inside the lugs. Metal straps are more difficult to put on the lugs, sometimes leaving unnoticed scratches.
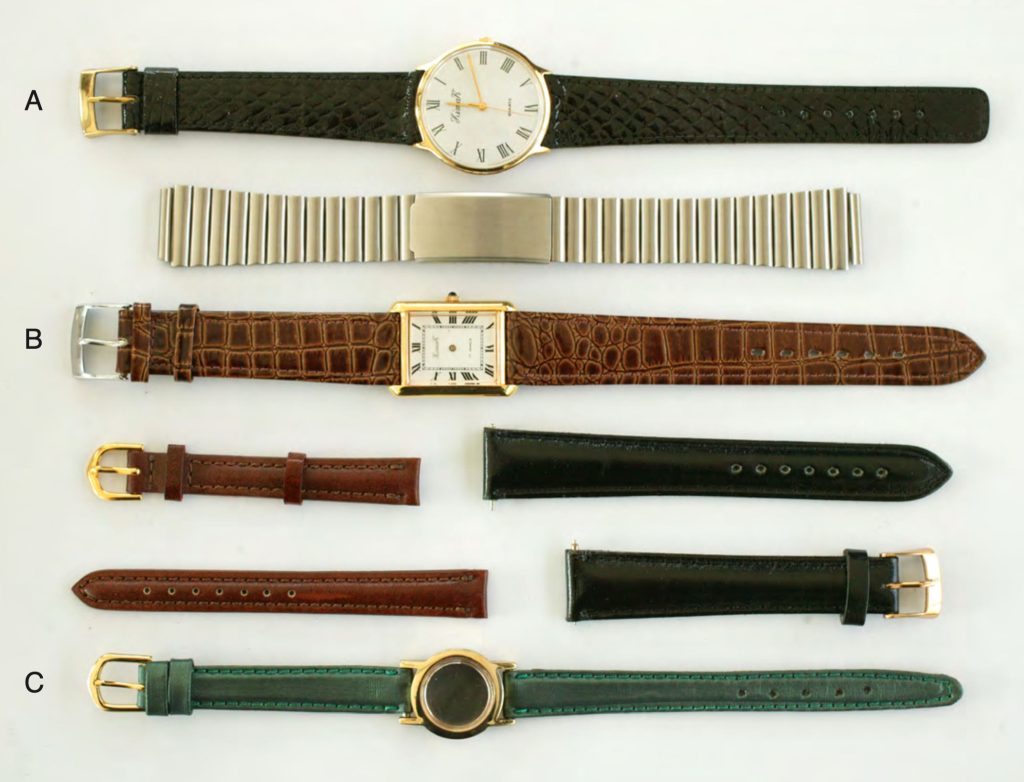
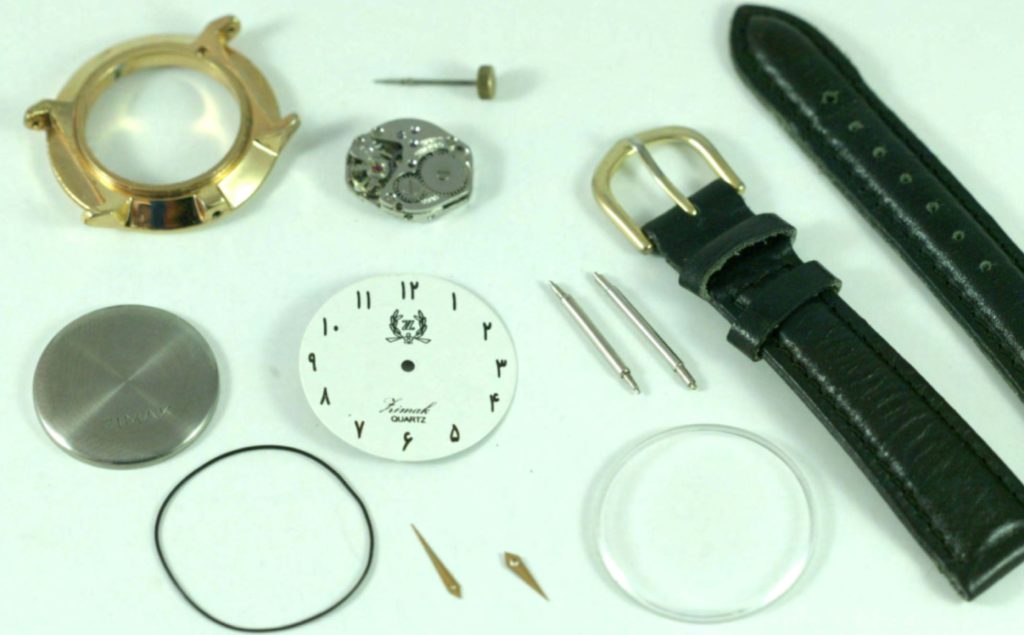
Men’s watch with mechanical movement, and Farsi numerals with Zimak’s logo, stainless back, and leather straps. Below, the polishing department uses polishing tools such as Lorch to polish various watch components before plating.
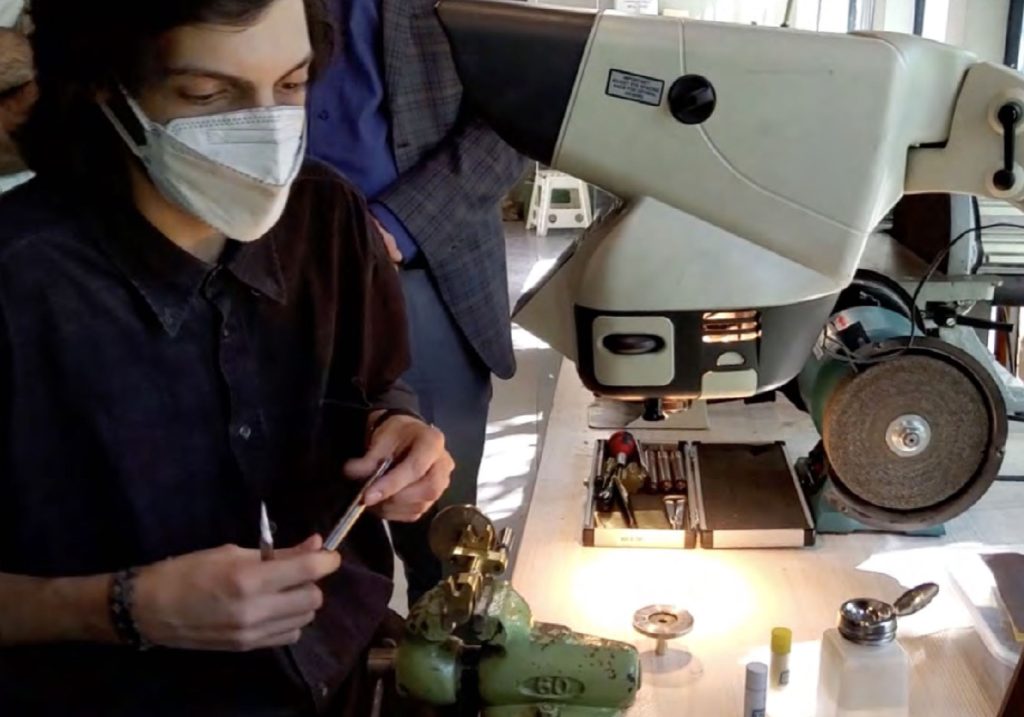
7 Cover Crystal
The cover crystal protects the watch dial, and its the main window to see time.
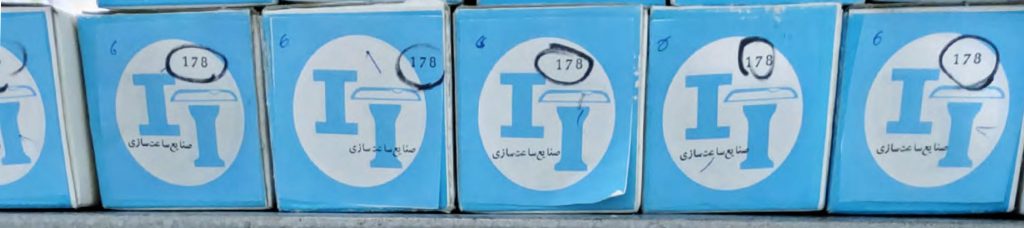
Watch crystalls with designation 178 stand for 17.5 mm diameter
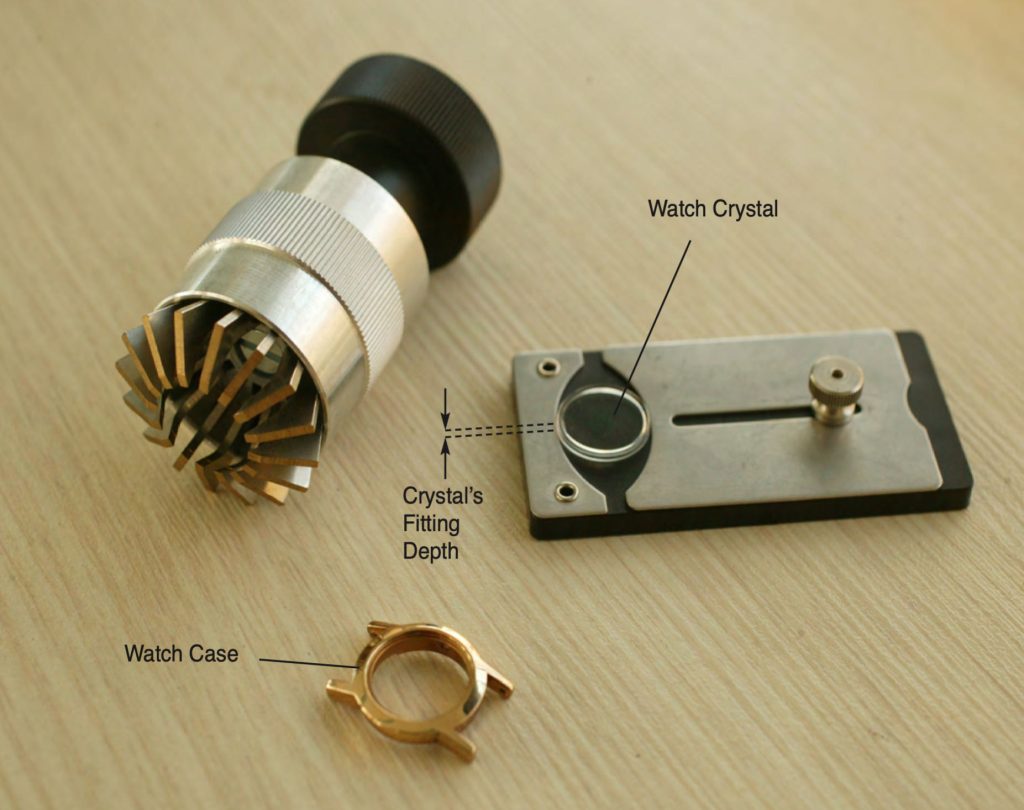
Watch cover crystals (above) are closely matched with their seating diameter on the case (below). The numeral 178 on each box stands for 1.78 mm (opposite page). This is the outer diameter of the crystal that would mount on front face of the watch, closely above the dial. For larger diameter watches, the crystal is slightly squeezed (less than 0.1 mm) for its insertion. For ladies’ watches, the crystal has less tolerance to fit in its place. To install the crystal, it is grabbed from a stand-off plate (below left), then transferred to the watch case (right), and the squeeze pressure is released.
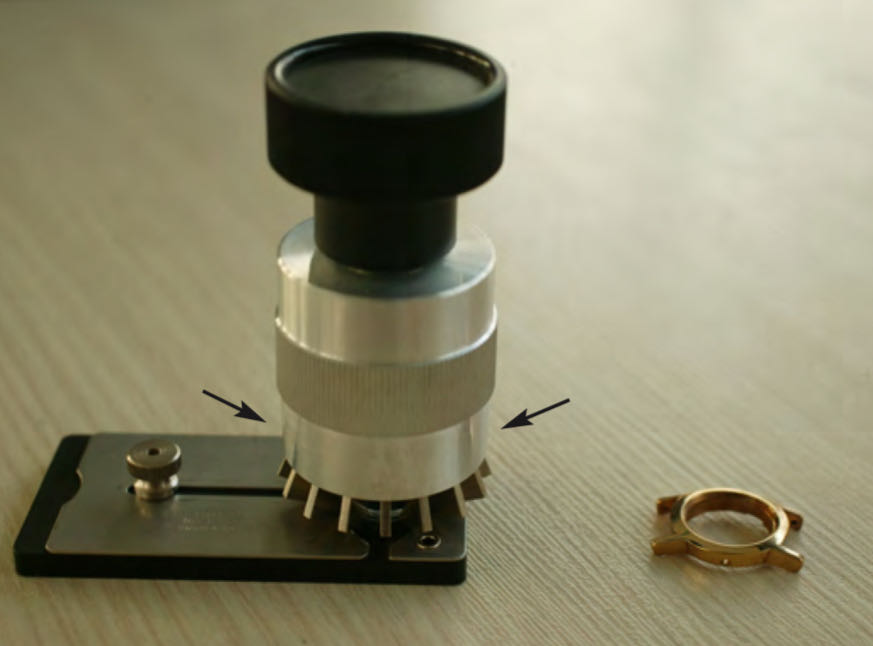
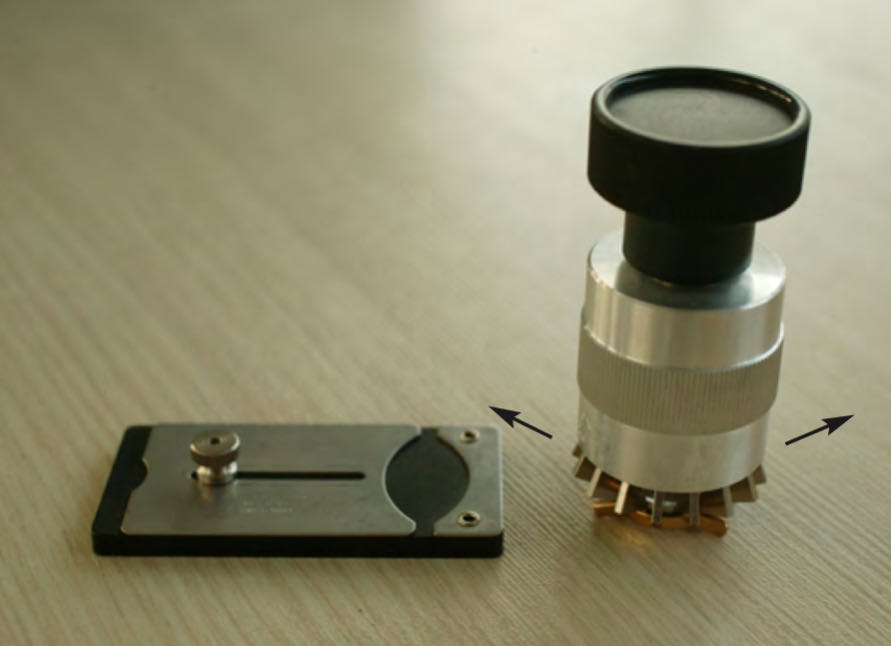
8 The Back Cover
Back cover is the user interface for minor repairs, and its bat- tery replacement. It protects the watch against moisture.
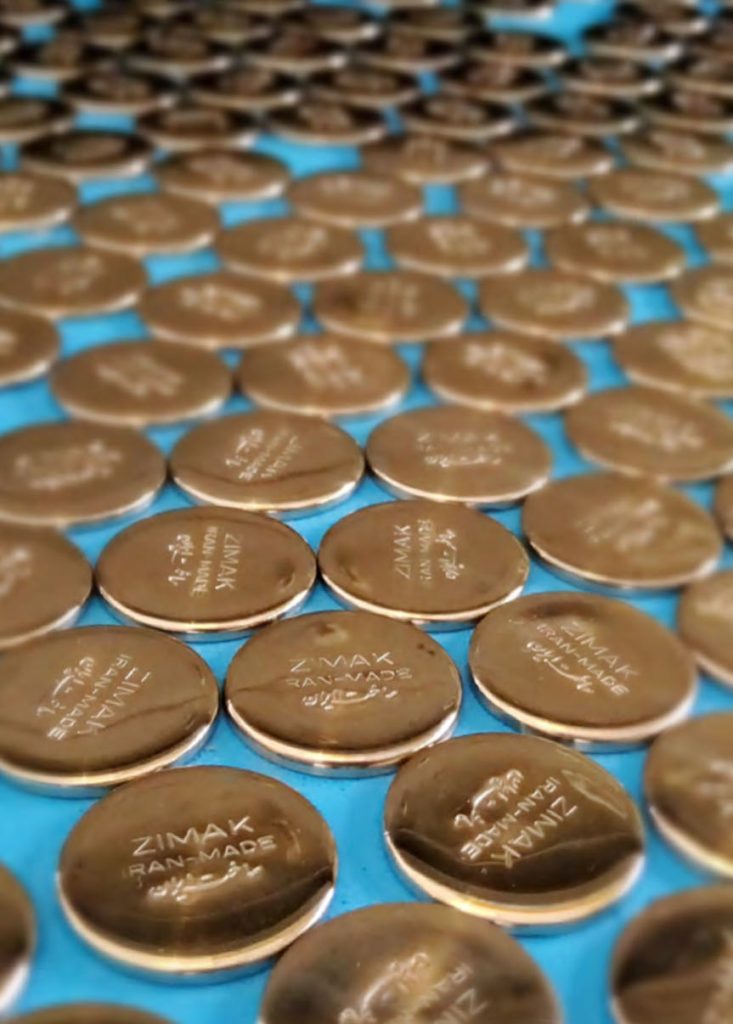
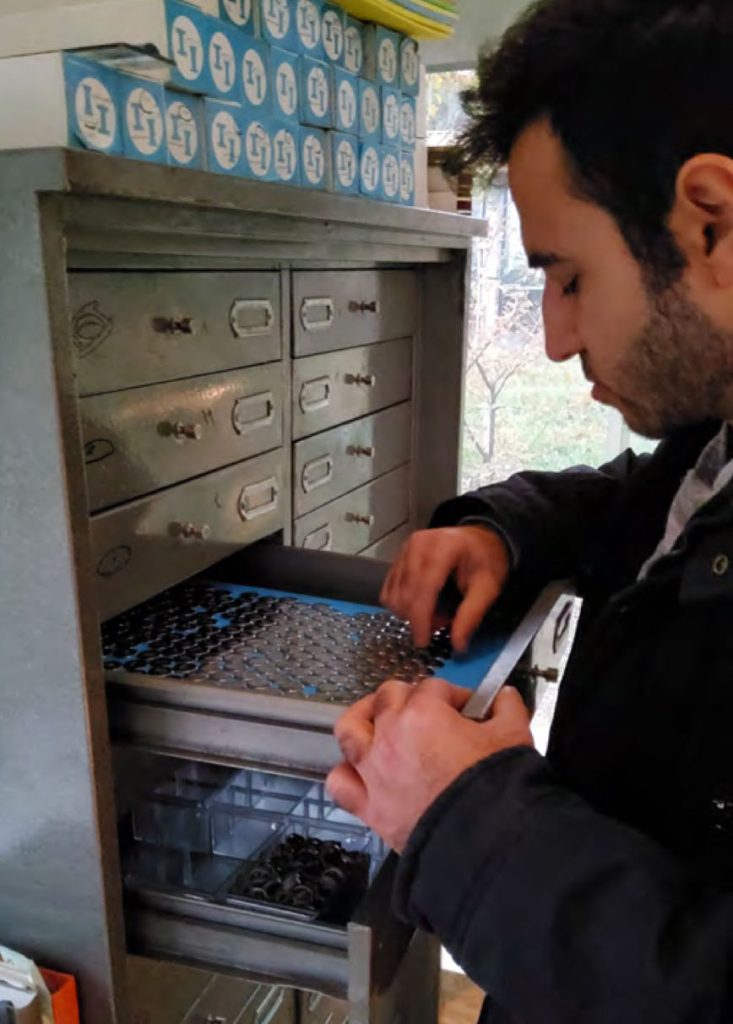
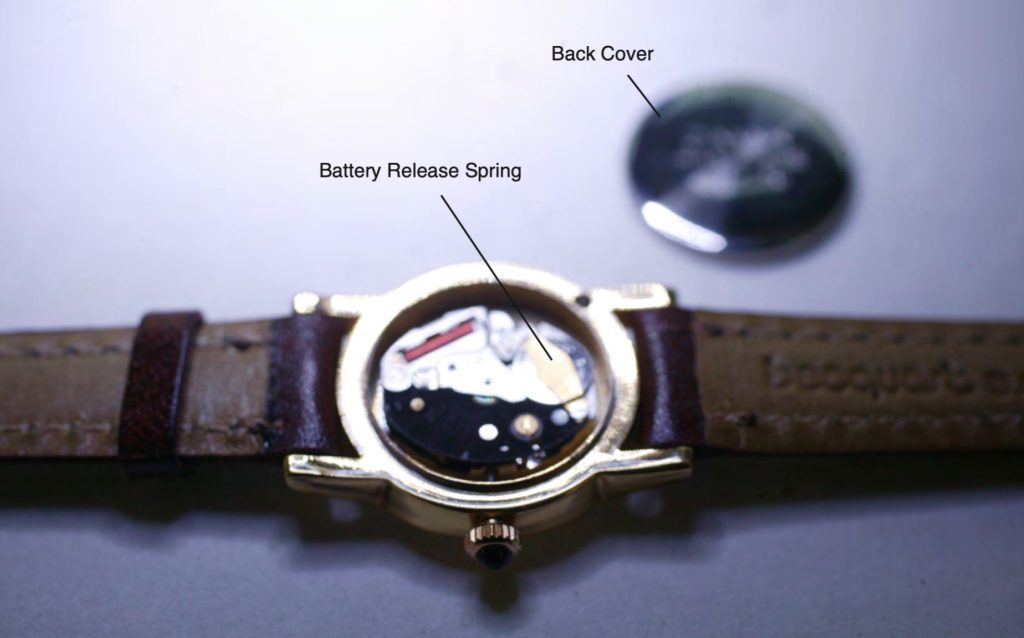
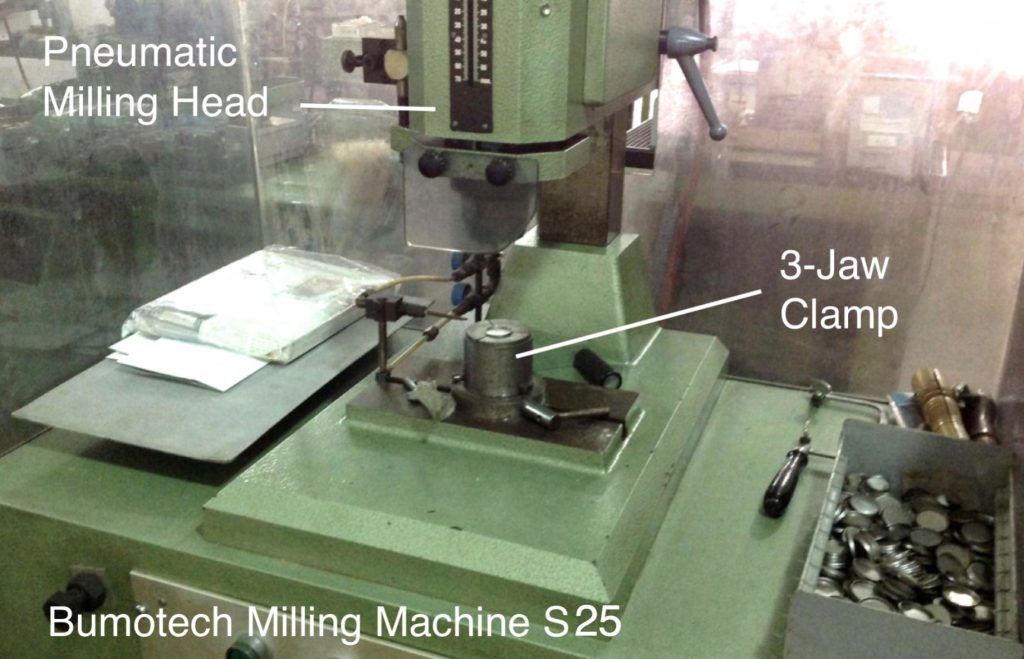
Bumotec S25 performing back cover milling to fit on back of the wrist watch. The 3-jaw clamp, and spring loaded plunger prevent the back cover from flying off during machining.
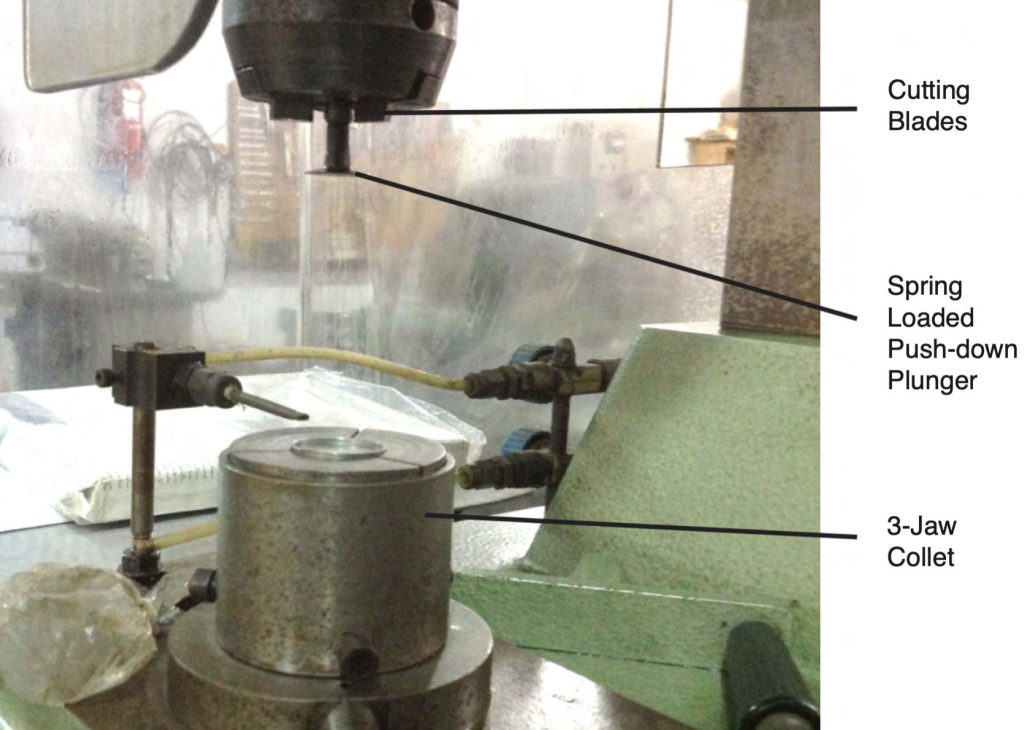
It’s not possible to be a watchmaker without enjoying classic art, and not to participate in its maintenance, and repairs.
An important part of mechanical watches and clocks is its hand polish, requiring good understanding of metals, various protective coatings, and sufficient experience with polishing materials. The most ordinary mission in classical watchmak- ing is making replacement parts, using specialized tooling. When pocket watches without Inca Block (a shock absorbing washer) are dropped, they are prone to bending of balance wheel pivot, or its breakage (below, left). A pivot polisher (next page) is ideal for such tasks. Main spring replacement (below, right) is also a common repair.
We will follow a routine clock repair on the next pages (28-29), and making a replacement pin for its pin escapement.
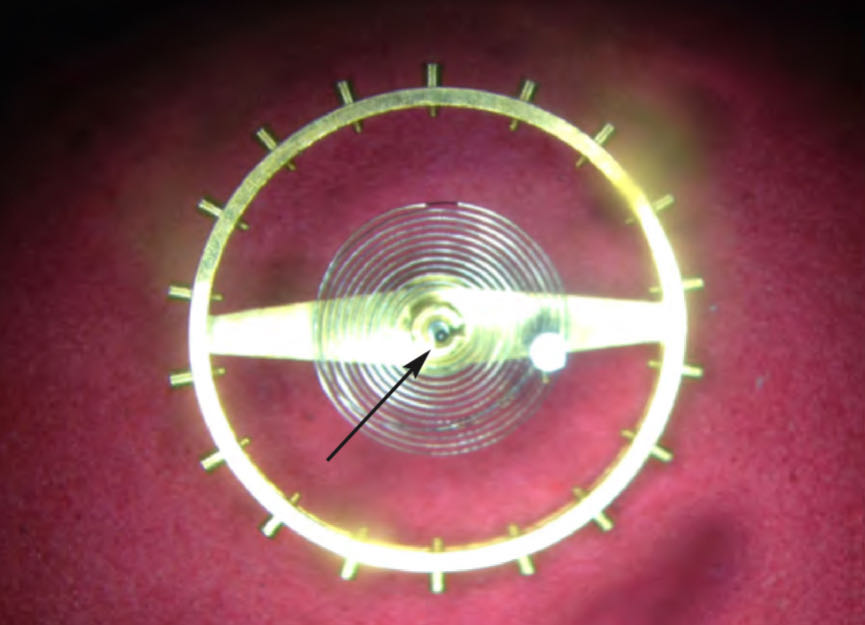
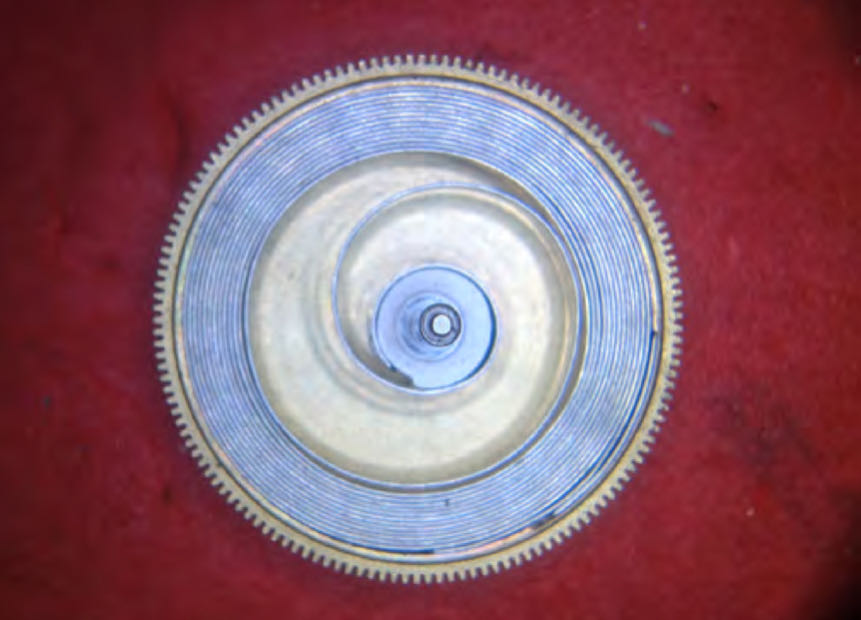
Center pivot of balance wheels (left) may easily break during a drop specially in pocket watches without an Inca Block.
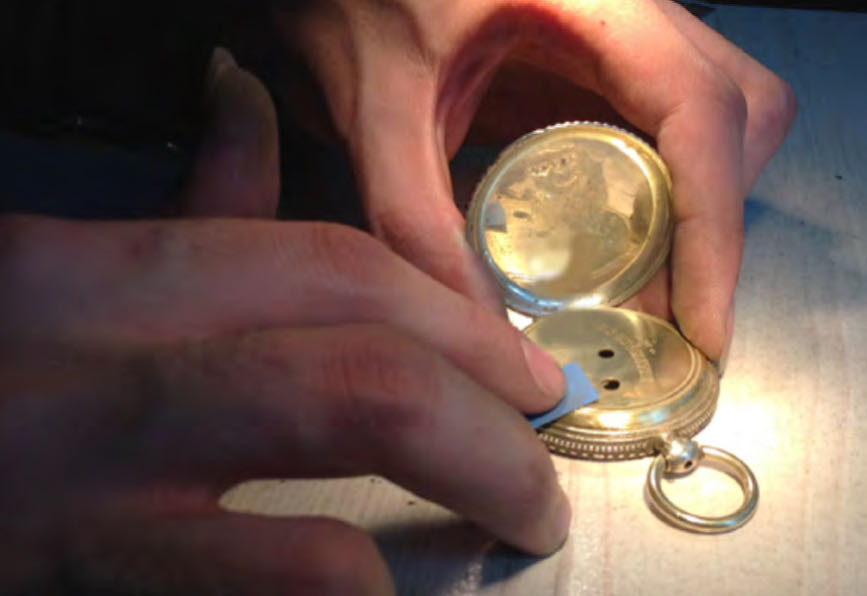
Hand polishing the case of a pocket watch
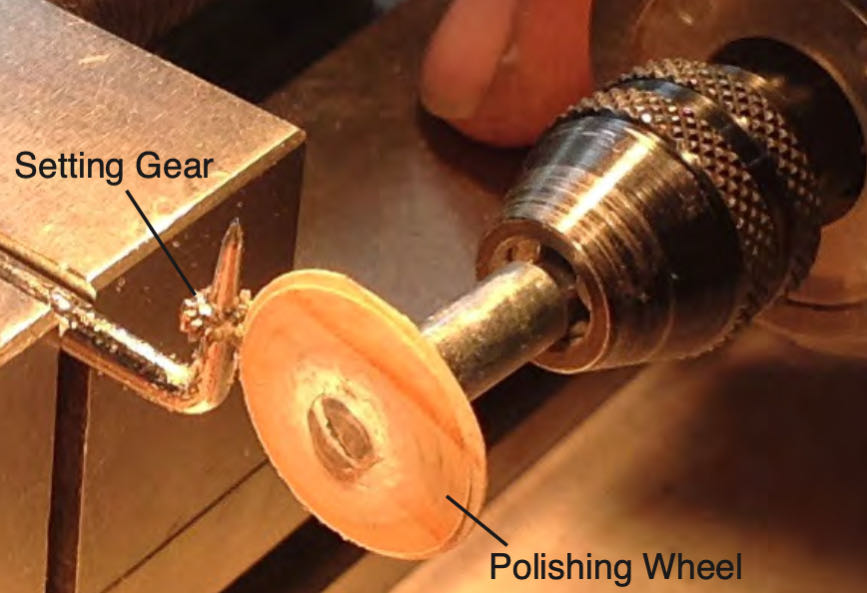
Polishing a tiny gear by grinding wheel made of cider wood
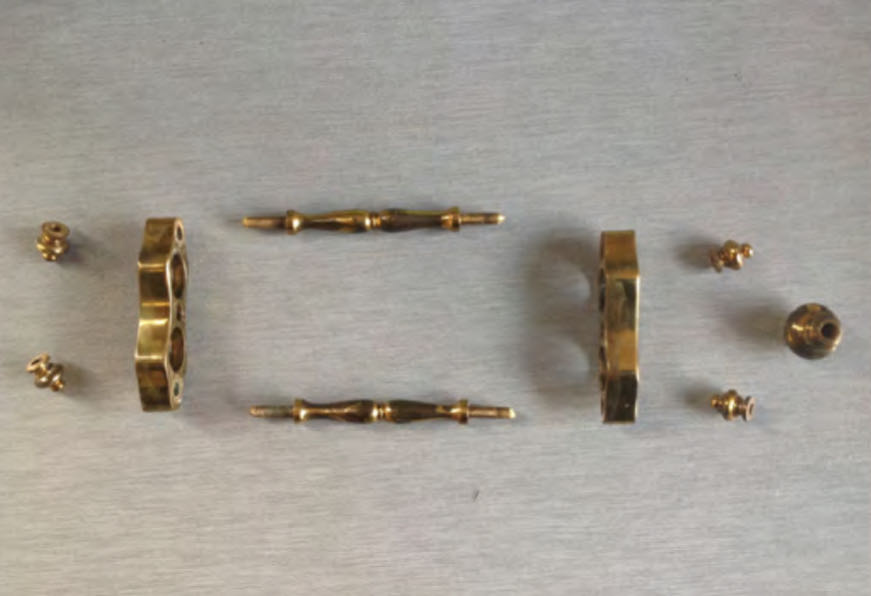
Woslon & Powel Pendulum (P 28, 29) before polishing
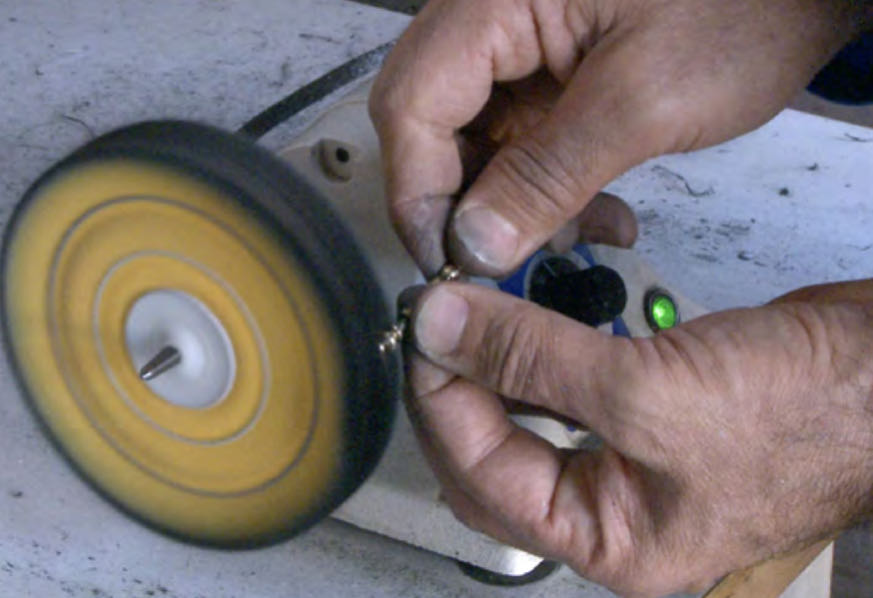
Hand polishing the Woslon & Powel Pendulum
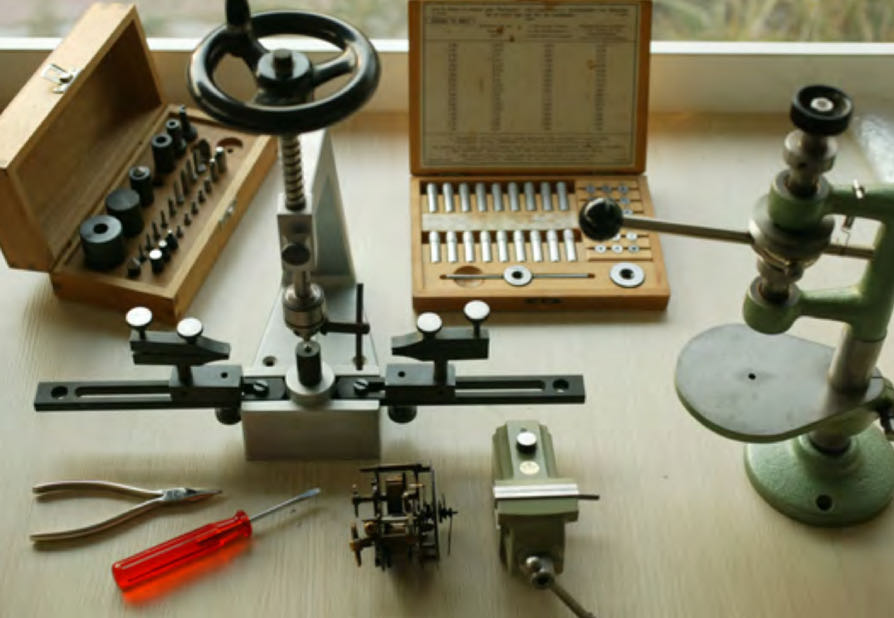
Small parts machining for desktop, and antique clocks.
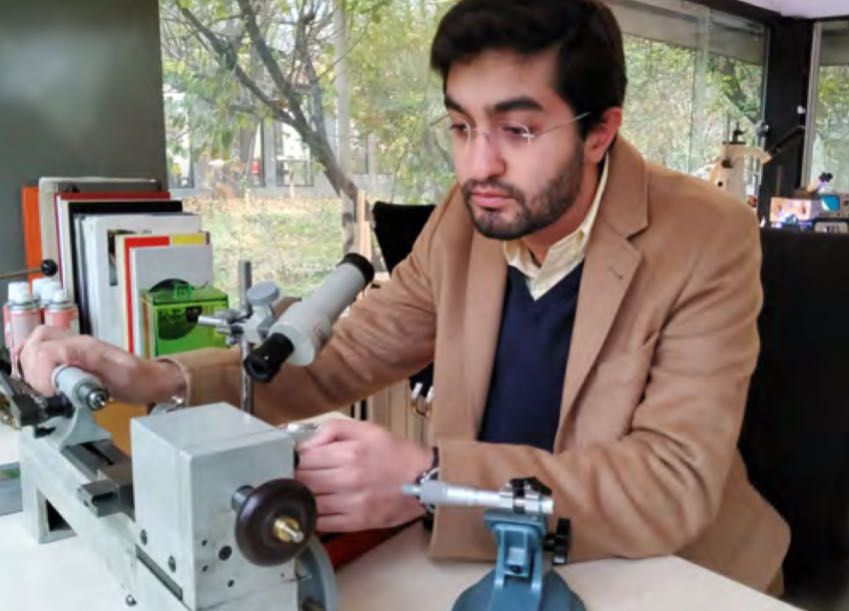
Watch case modifications on Levine lathe
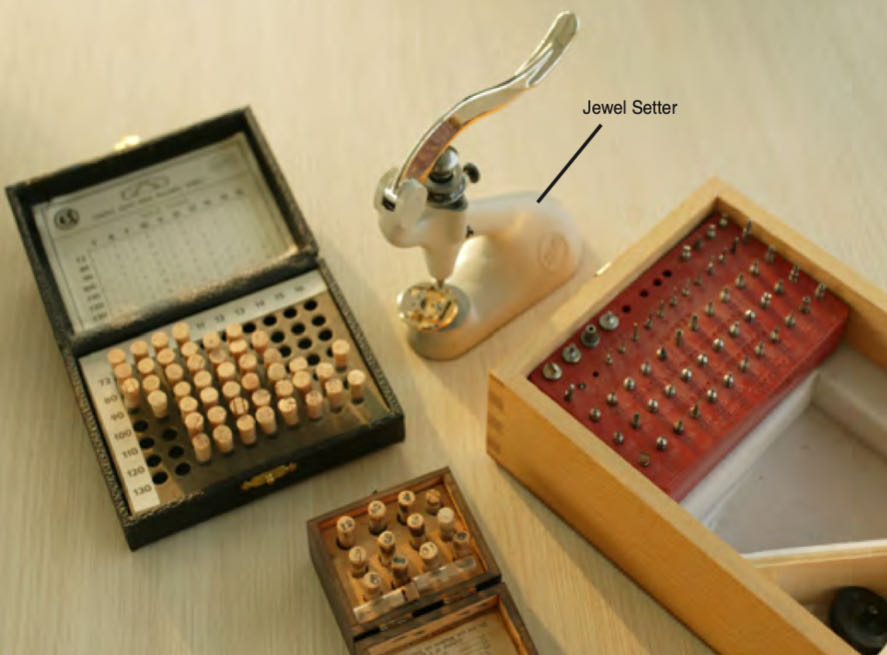
Jewel setting the mech plate of a wrist watch
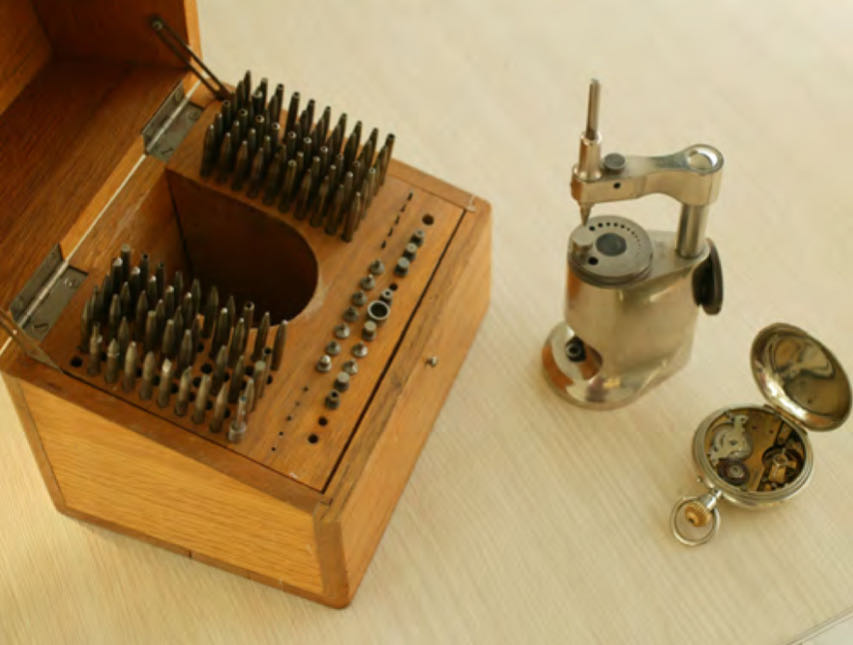
Tightening the mounting bore of a watch hand by punching
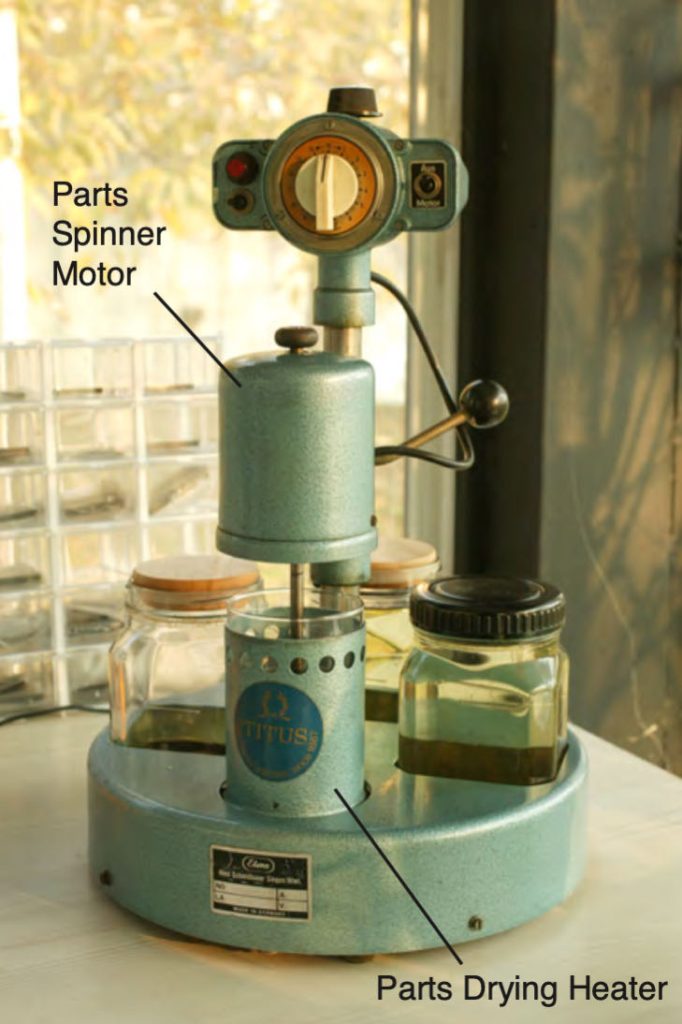
Elina Parts Washer
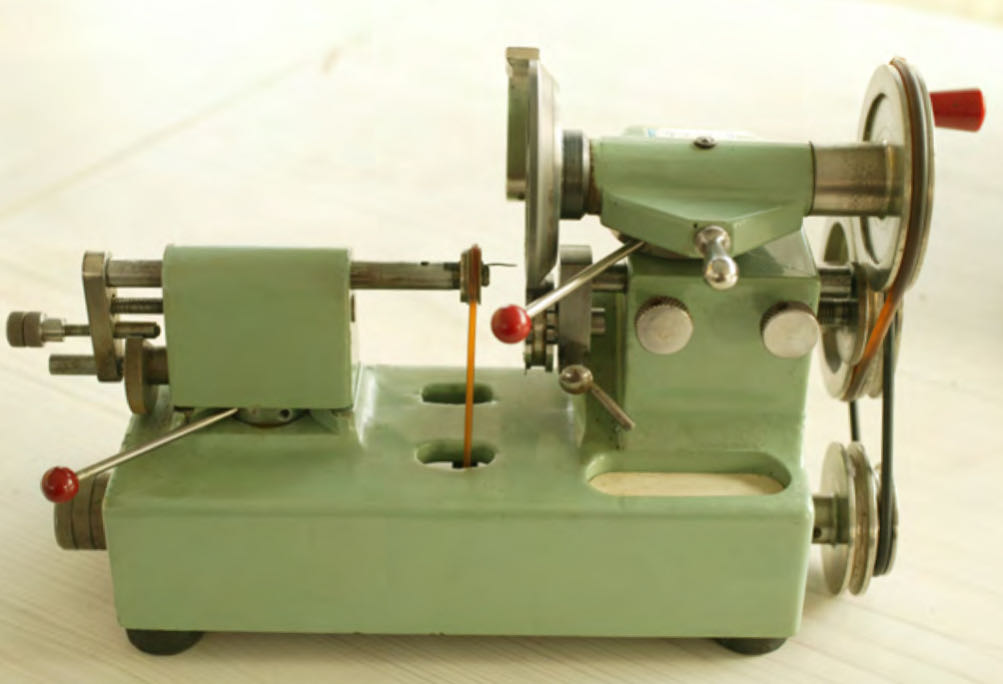
Pivot polishing the balance wheel of a pocket watch
Watchmaking takes so many special tools, and it would take discipline to actually use them. Some watchmakers unfortunately get the habit of using the tools that are nearby their workstation. It takes a good floor manager to establish professional habits among his staff to be using the right tool for the right task. Some tools are avoidable to use from time to time, such as the pivot polisher above, and specially the precision Levin lathe.
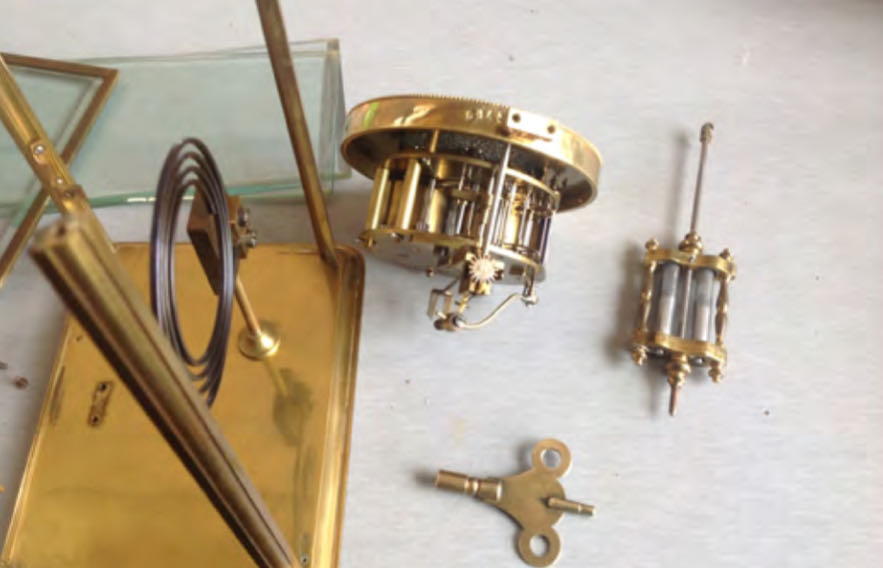
Repairing a French made Woslon & Powel clock
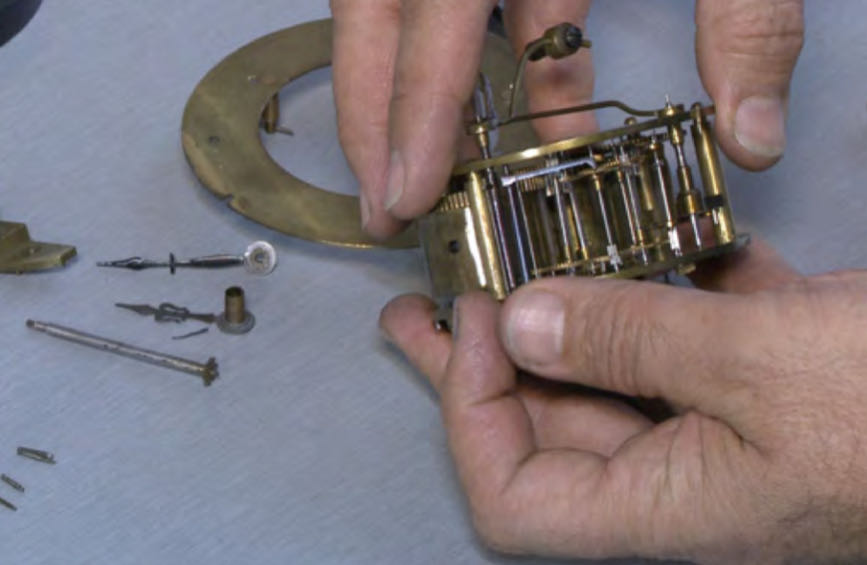
Dismantling the clock for complete overhaul and repair
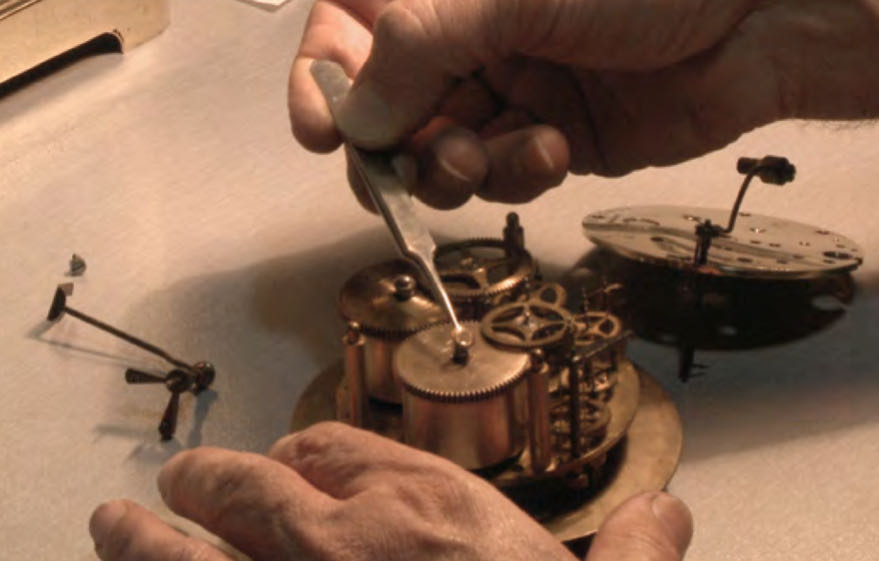
Removing the spring box for cleaning and lubrication
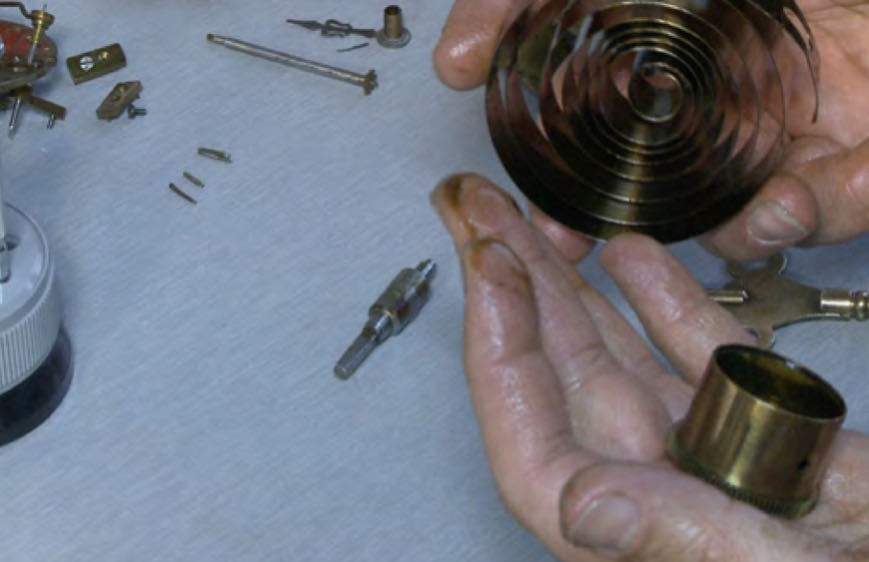
Remake of one of the broken spring hooks
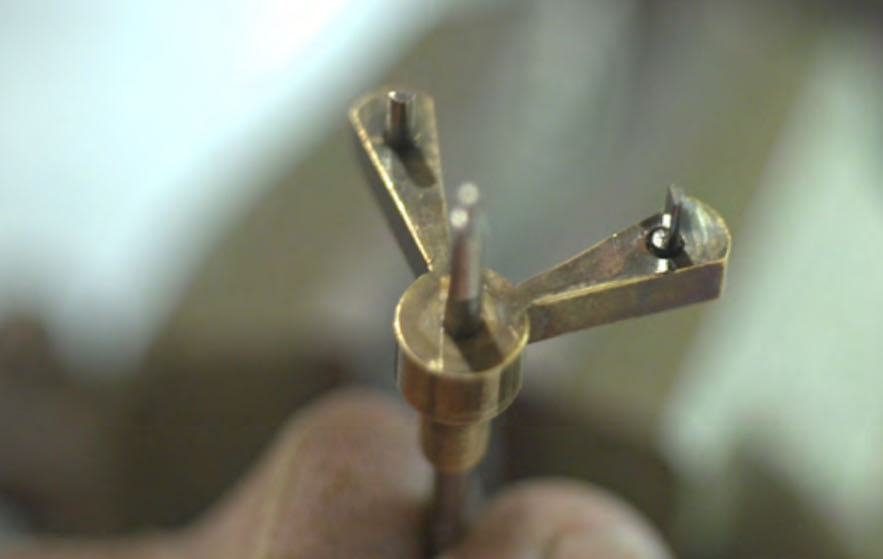
One of the pallet pins needed replacement
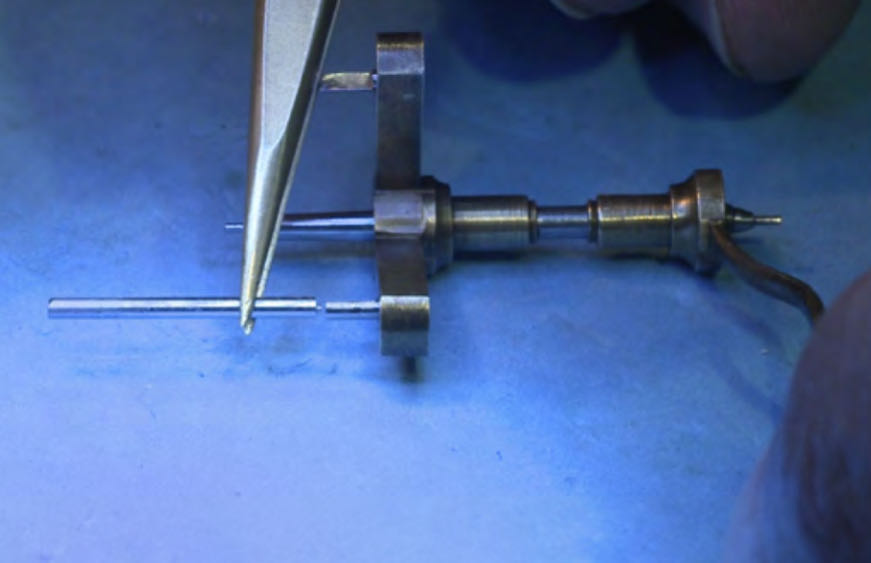
Pallet pin was matched with stock steel for fabrication
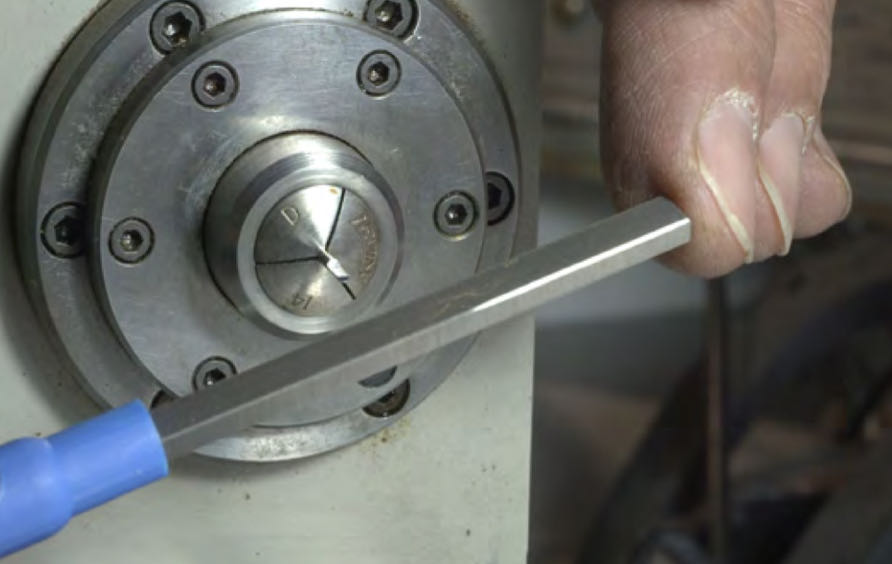
The rod was machined using Levin lathe, and mill
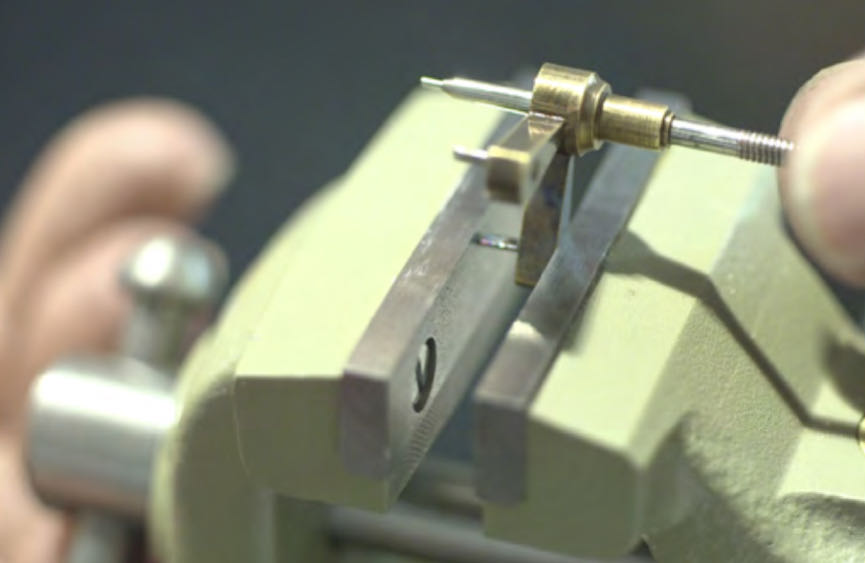
New pallet pin was replaced after hardenning, and anealing
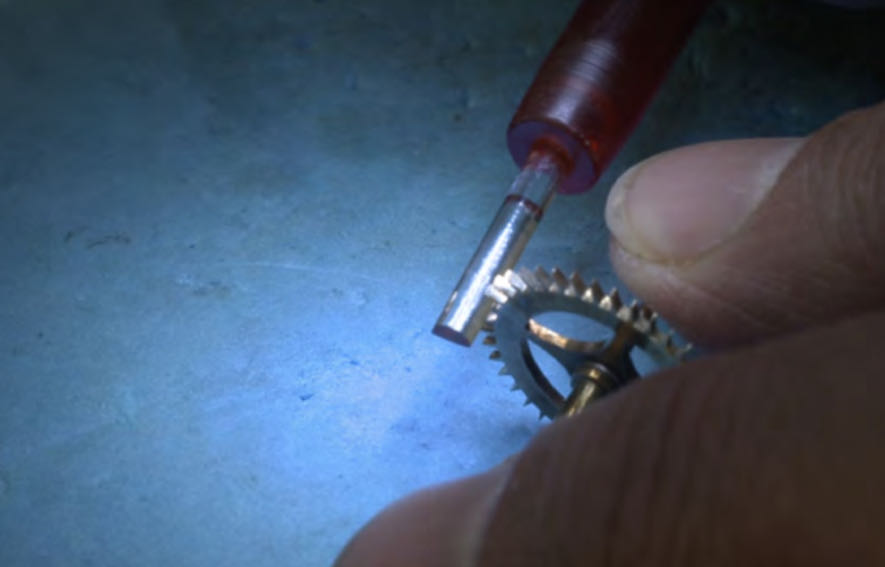
Fine polishing the pallet wheel with a saphire file
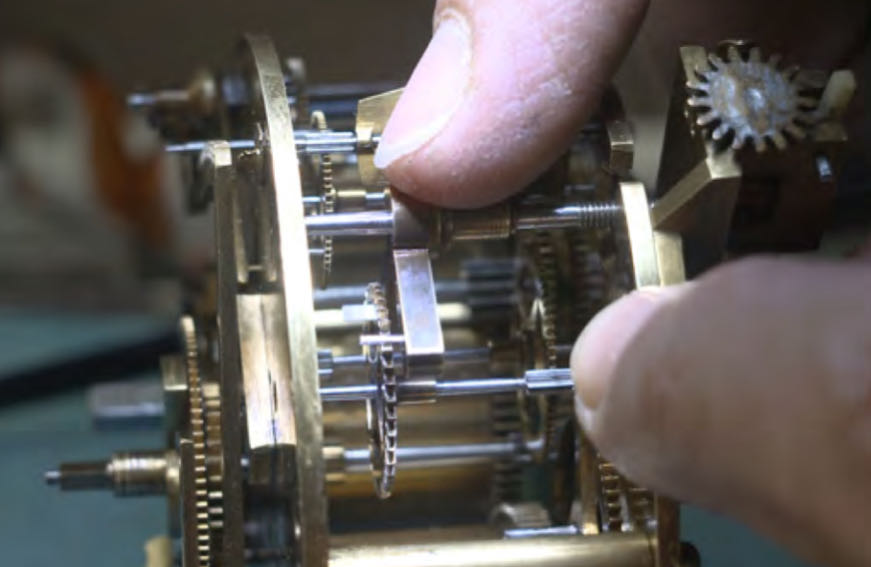
Installing the refurbished pallet, and pallet wheel
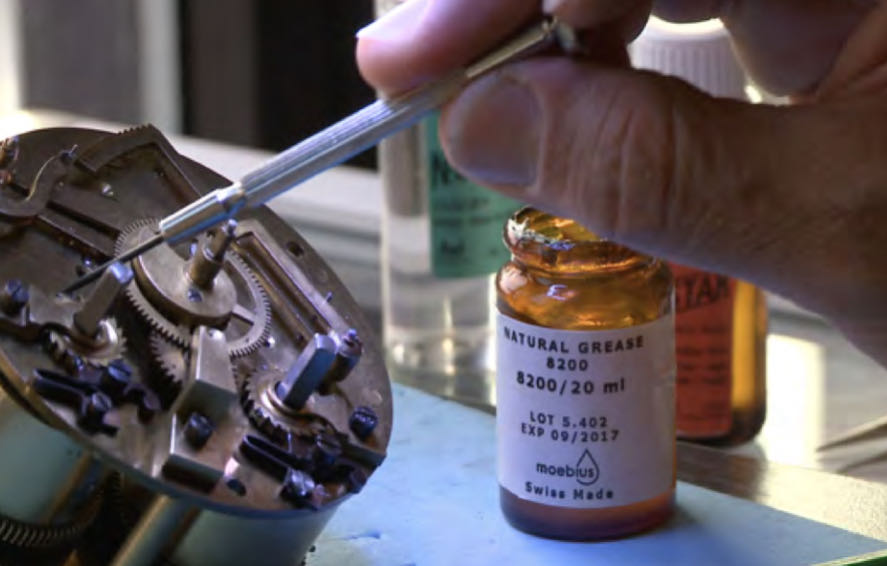
Appropriate lubes are applied to all moving parts
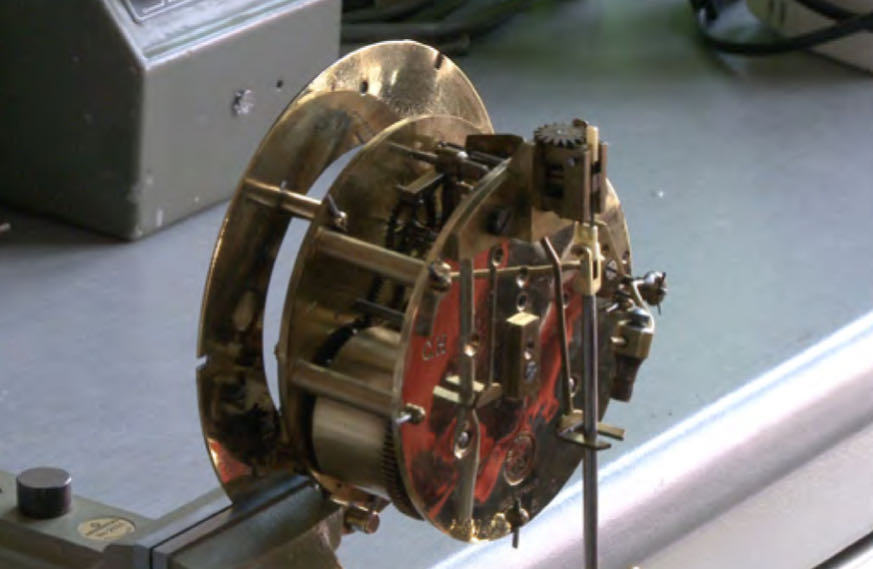
Testing the clock by letting it to run for a few days
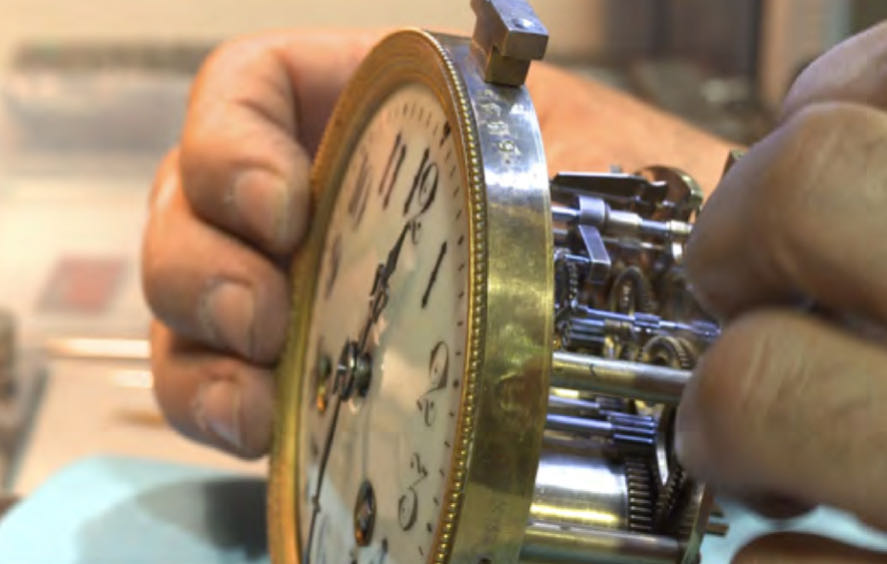
Reassembly of the dial, and the hands
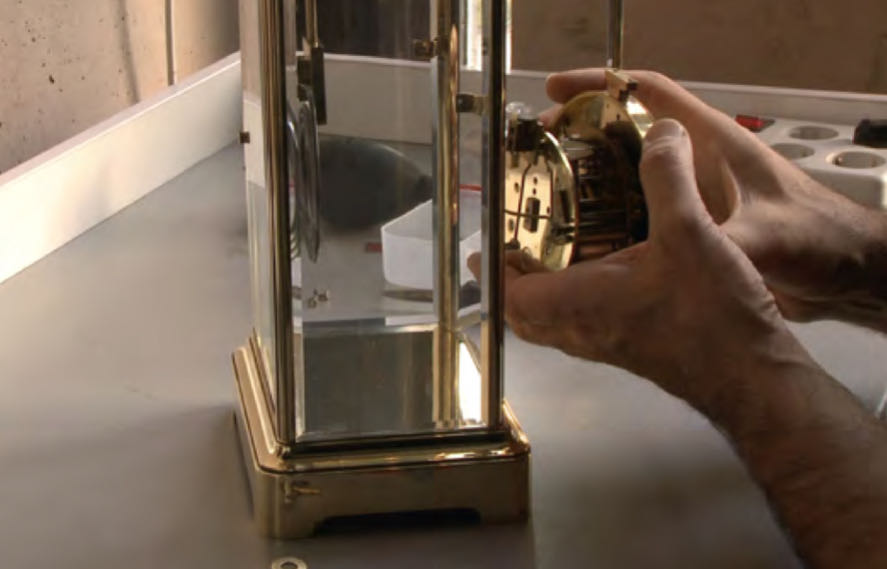
Reinstalling the movement on the main housing
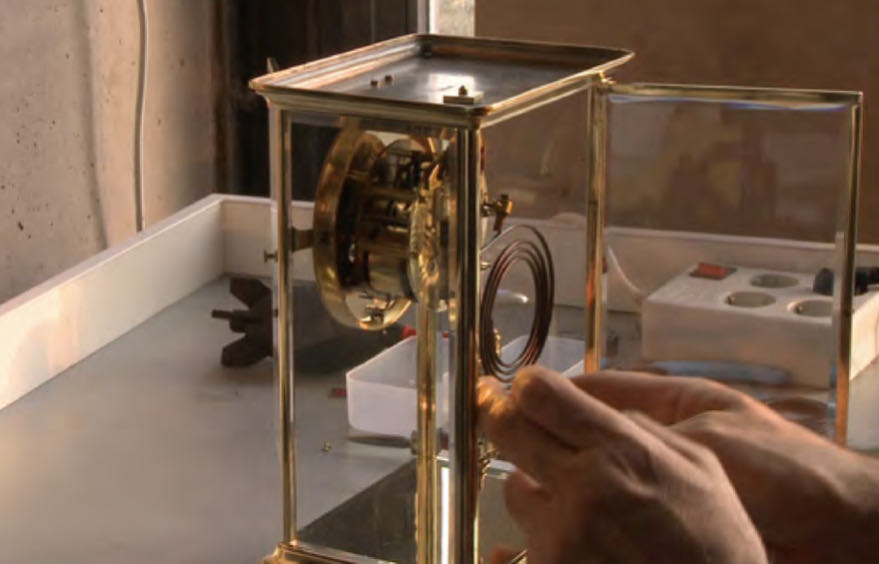
Installing the polished pendulum, and the helical chime
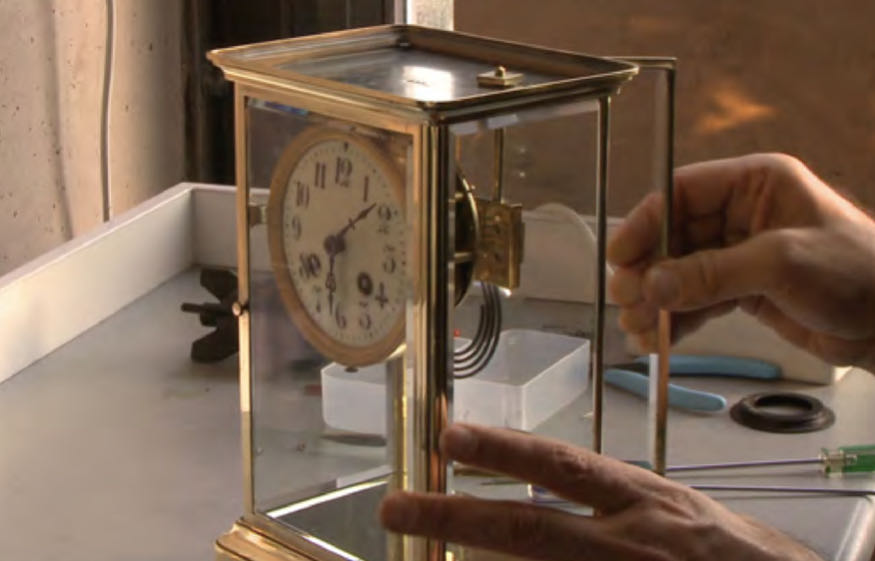
Woslon & Powel clock after polishing, and full maintenance
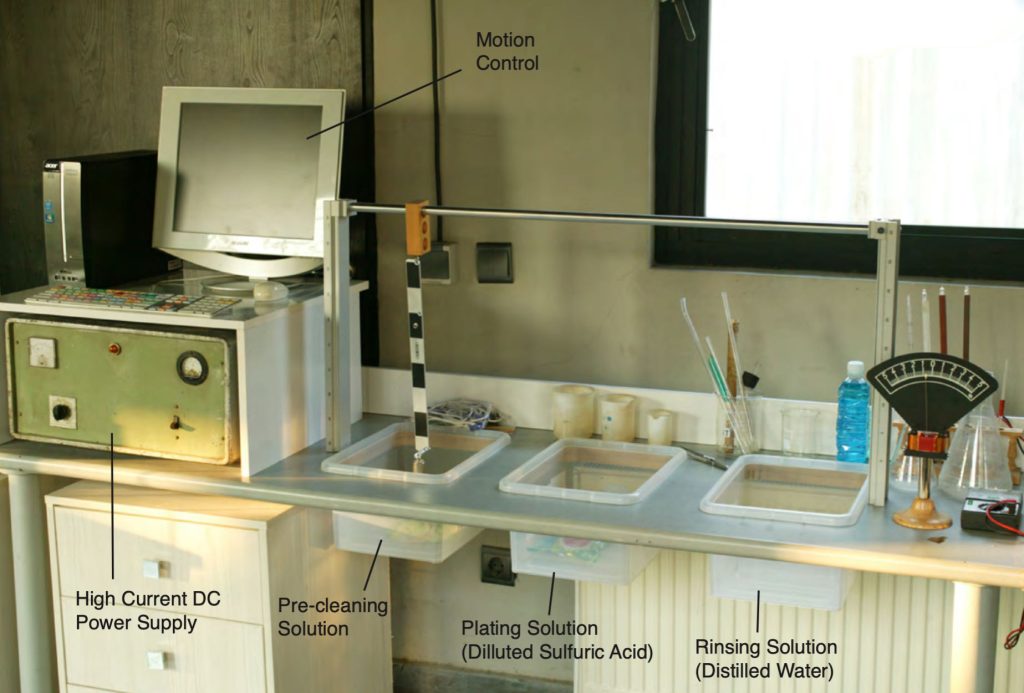
Watch cases, and all fabricated parts that are non-stainless receive a 5 micron thick coating inside plating tanks with Gold, Nickel, and other metals. Gold plated parts are further plastic coated to prolong their life against normal sweat on the wrists.
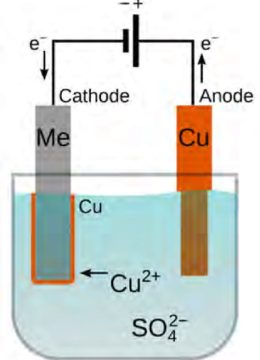
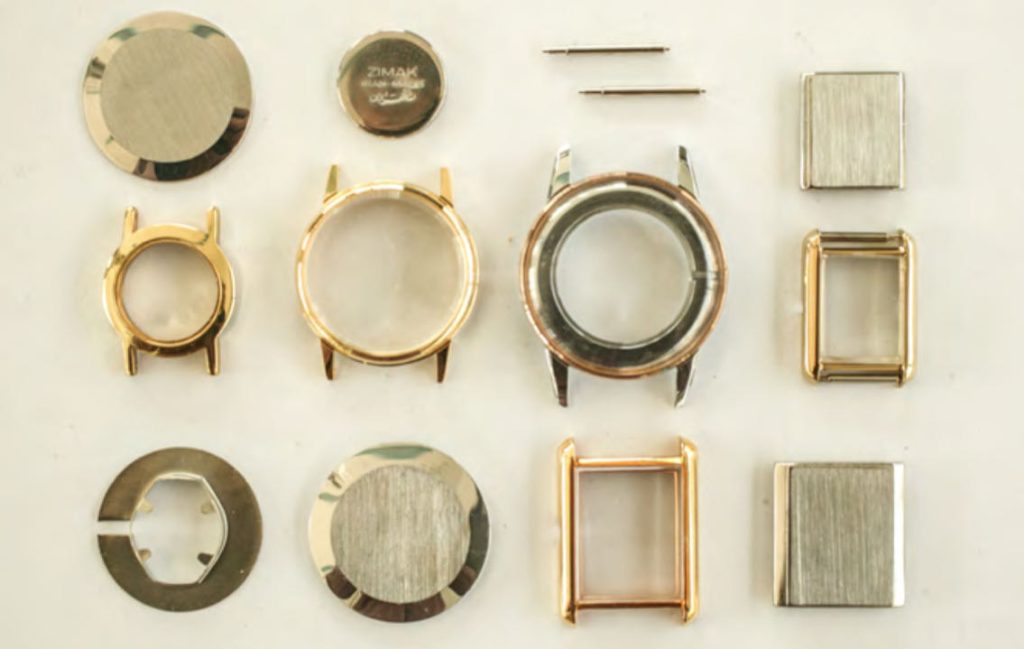
Plating is the process which electrically conductive surfaces are coated with metals. Parts are immersed into a metal salt such as diluted Sulfuric acid, and a high current DC power supply establishes an electric current between an anode (in this case Copper, Cu), and the immersed parts (Me), hanging on a rack (Cathode). The anode is the material that is consumed during the coating. During the electro plating process, posi- tively charged Copper ions are migrated from the surface of the Copper plates to the cathode, hence coating the parts. The longer this process takes, and higher the current, the thicker the coating. The surface area of the Anode must be higher than the total surface of the parts being coated.
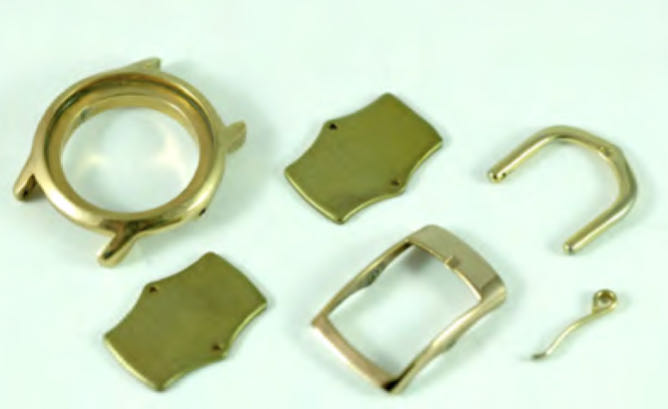